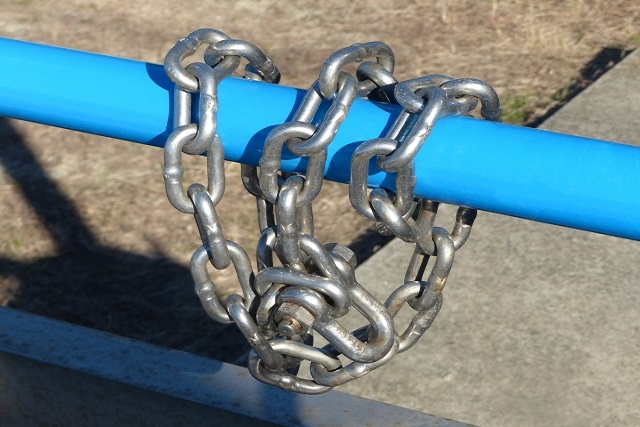
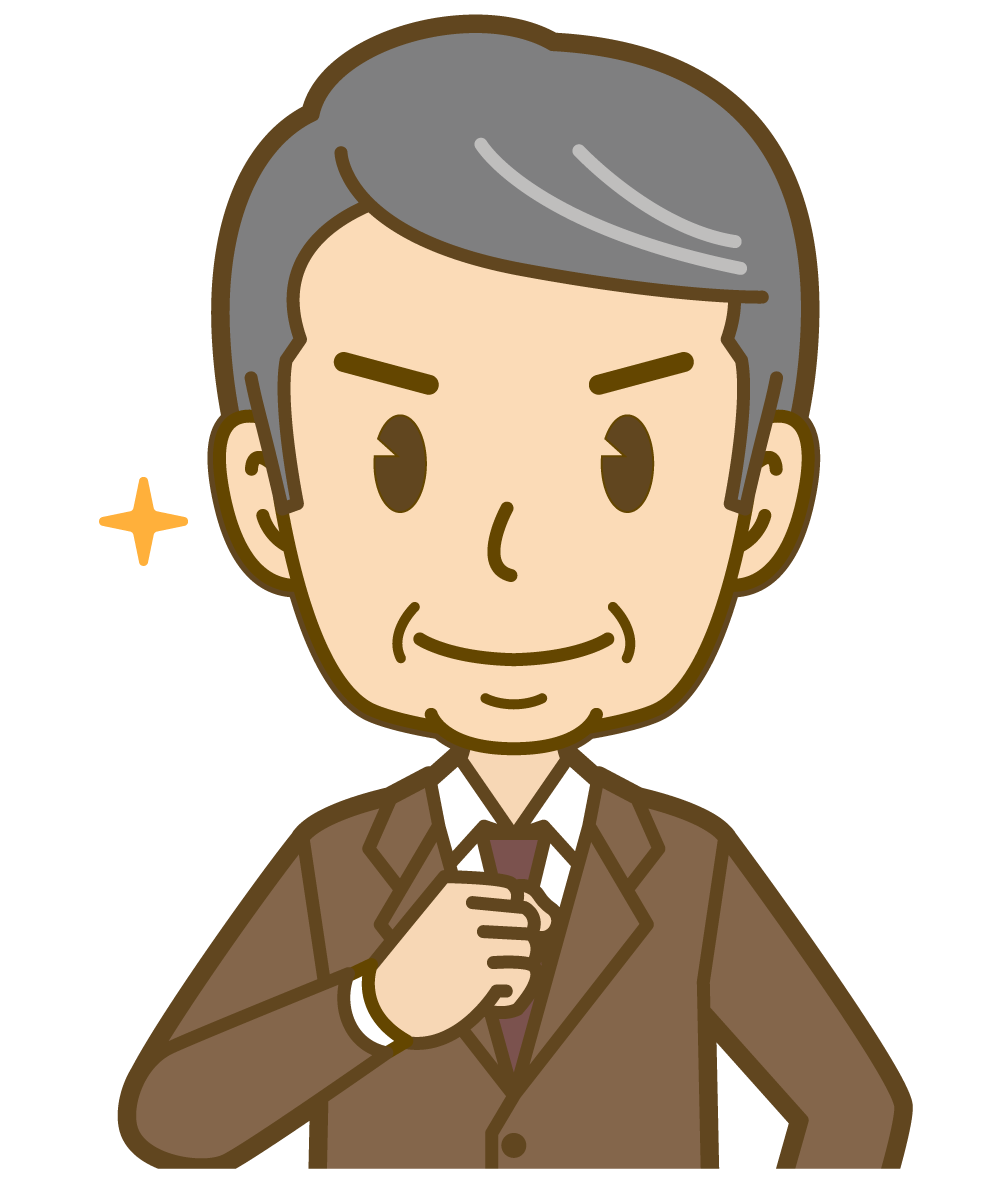
What is TOC (Theory of Constraints)? What does it mean to apply TOC to product development?
The Goal” was published in the U.S. in 1984, and TOC (Theory of Constraints) quickly spread throughout the U.S. and from the U.S. to the rest of the world. (The Japanese edition was published 17 years later.) Initially used as a problem-solving method in production, TOC gradually came to be used in a variety of situations within companies, and many companies in ・Japan also began to utilize TOC. What is TOC again? We will explain what we mean by “applicable in product development.
Based on our experience in supporting reform of product development organizations using Lean product development and job theory, and our experience in introducing and implementing the TOC (Theory of Constraints) thinking process into reform strategies, we will review the TOC concept again and explain how it can be applied in product development organizations.
Contents of this article
What is TOC?
The Theory of Constraints (TOC), said to have been developed by Dr. Eliyahu Goldratt, an Israeli physicist, originally arose from his development of software for scheduling in a production plant.
The novel “The Goal,” which was written to explain the software developed by Dr. Goldratt in a way that could be easily understood by many people, became a huge hit, and TOC spread throughout the world.
The basic concept of TOC is that the common goal in all companies is defined as “to continue to make money from the present to the future,” and by concentrating on improving the constraints or bottlenecks that prevent the company from achieving its goal, the company system is improved so that the overall company performance, or throughput, is increased.
To give a very simple example, if there is a factory line as shown in the figure below, and the production capacity of each process is different, the production capacity of the entire factory will be limited by the process with the lowest capacity (process 3 in the example).
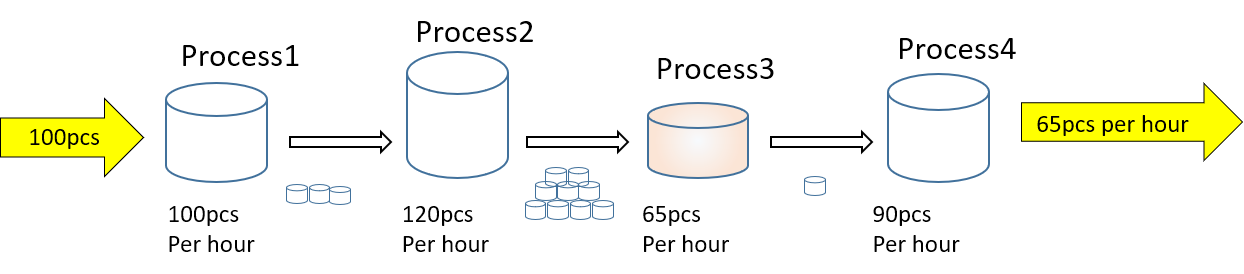
Even if you try your best to improve each of the processes and increase the capacity of each individual process, if the capacity of process 3 does not change, the capacity of the entire factory will not change.
The first teaching in TOC is that a company’s mistaken improvement activity is to spend effort on individual partial optimization without looking at the overall throughput.
This example is so simplistic that I don’t think anyone would not understand it, but how it works in a real company is not as simple as the example, but the tasks and functions are connected between organizations in a company, even outside of the factory.
So all corporate activities have inputs to outputs, just like in a factory, and the throughput may be limited by constraints, or bottlenecks.
This means that unless we look at the whole picture and make improvements, there is no point in only making improvements in individual organizations.
There are many great ideas in TOC, but one of the things I like most about it myself is that if we can accurately grasp the constraints, or bottlenecks, and make improvements, we can see the effects relatively quickly.
However, it is also important to continue improvement activities based on TOC.
Constraints, or bottlenecks, change with improvement activities or due to the influence of environmental changes.
Therefore, it is important to continue improvement activities while carefully monitoring the situation.
What are constraints?
In the theory of constraints, we will consider three constraints.
Physical constraints
These are constraints such as capacity within a company. These are physical constraints, such as the capabilities of machines in a factory or the capabilities of people and organizations, which are also mentioned in “The Goal.”
Market constraints
A constraint between a company and the outside world, such as an imbalance between the supply capacity of the company system and market demand.
Policy constraints
Organizational problems that tend to occur are those caused by dilemmas between the major policy of top management and the minor policies and decision criteria of each department, which in the TOC are called policy constraints.
Each of these three constraints can be closely related to each other.
In the TOC, we start with the fact that it is one or very few constraints that limit the throughput of the enterprise system, and we continuously improve the enterprise system through the following five improvement steps.
- Identify the constraints
- Determine a policy for thorough utilization of the constraints
- Match non-constraints to constraints
- Strengthen the constraints
- Return to the beginning when the constraint is resolved
Logical thinking that captures the essence of the problem -Cloud
TOC’s enterprise system improvement framework is also called the Thinking Process.
In other words, the TOC framework provides a logical way of thinking.
So, logical thinking is very important for the TOC framework to work well.
As a premise of the TOC Thinking Process, we believe that almost everything that happens in a company is connected by a cause-and-effect relationship, i.e., because XX, △ △ △ △.
In a sense, we might say that the improvement process is about deciphering this cause-and-effect relationship.
Also, within the TOC framework, a tool called cloud (see below) is used.
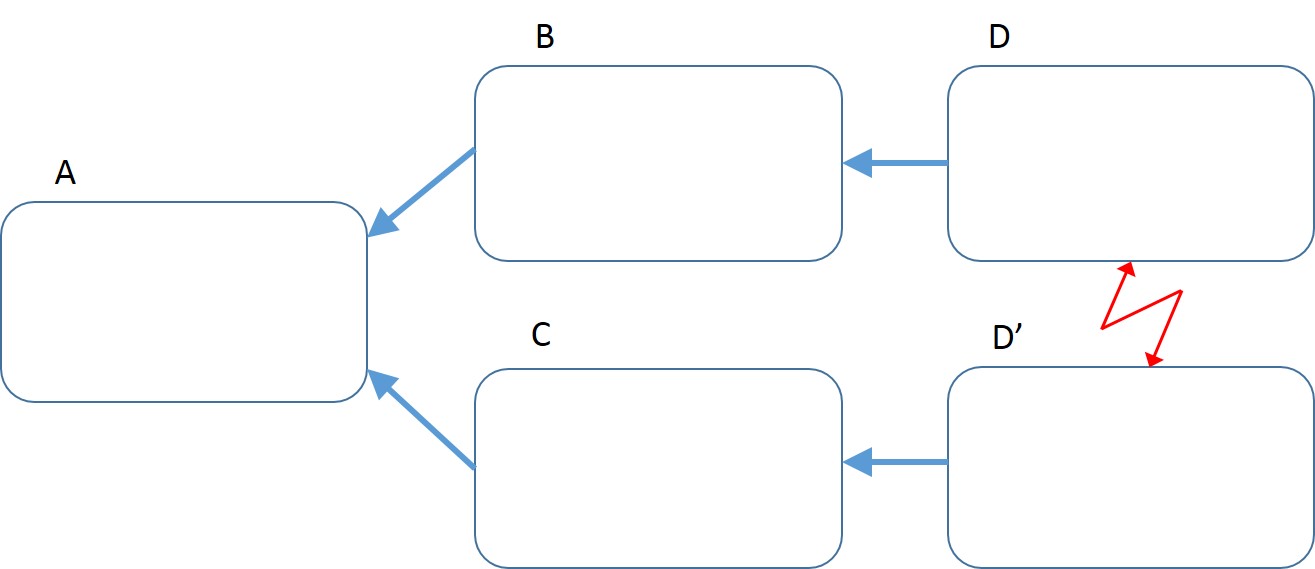
In Japanese, it is called a “conflict resolution diagram, and” it is a tool to objectively, simply, accurately, and free from assumptions about the mechanism by which bad symptoms (which can also be read as problems) occur in an organization.
Please refer to our other article “How to Create a Conflict Resolution Diagram” if you would like to learn more.
In order to master the TOC framework, you need to be able to make this cloud well.
The cloud is made up of necessary condition logic, which is a bit different from cause-and-effect logic, but the important thing is to have the ability to think objectively about the problem without putting in personal opinions.
If you are not used to this, you will end up creating a cloud with solutions and your own opinions, and you will not be able to solve the problem as it should be solved.
Consider that many people have trouble distinguishing between facts, hypotheses, and opinions in their minds.
When people are able to reaffirm the natural process of organizing facts, hypotheses, and opinions, correctly grasping the situation, and then making their own decisions (opinions), I believe that even people’s behavior will change.
I believe that cloud creation can be improved through repeated practice. (I am demonstrating this with various clients.)
Prerequisites for TOC
The beauty of TOC is that it is humanistic, or rather, we feel that it is thought out with a good understanding of the organizational field.
Among them are the following four assumptions that alert us to people’s assumptions.
- Things are simple to begin with.
Don’t complicate problems with ties and assumptions. - Organizational problems are not caused by bad people.
It is important to review assumptions, not to search for culprits. - There is always a win-win solution.
Don’t blame others for not being able to solve the problem. - Never say you’ve already figured it out.
There is no end to improvement.
In addition to this, Dr. Goldratt’s premise is that everything in the aforementioned companies is causally connected.
What is also very interesting is the idea that there are “six layers of resistance” within the organization that prevent problem solving.
- They do not recognize the problem they are trying to address as a problem.
- Disagrees with the direction of the solution.
- Do not believe the solution will solve the problem.
- The solution, if implemented, will cause negative impacts.
- There are obstacles that prevent me from implementing the proposed solution.
- Fear of the unknown that will result.
Does your company have any of these?
Have you given up on the idea that you have no choice?
Wouldn’t you consider that it is not the fault of the person resisting you, but rather that you have not been able to persuade them properly after all?
How do we persuade them? How do we help them see things on the same level? The TOC thought process is to think about and implement the following.
Strategic Approach
The TOC framework takes a strategic approach.
- What to change (what is the current problem)
- What to change to (how to set goals)
- How to change (how to solve the problem
The process of 1, 2, and 3 is strictly adhered to and implemented.
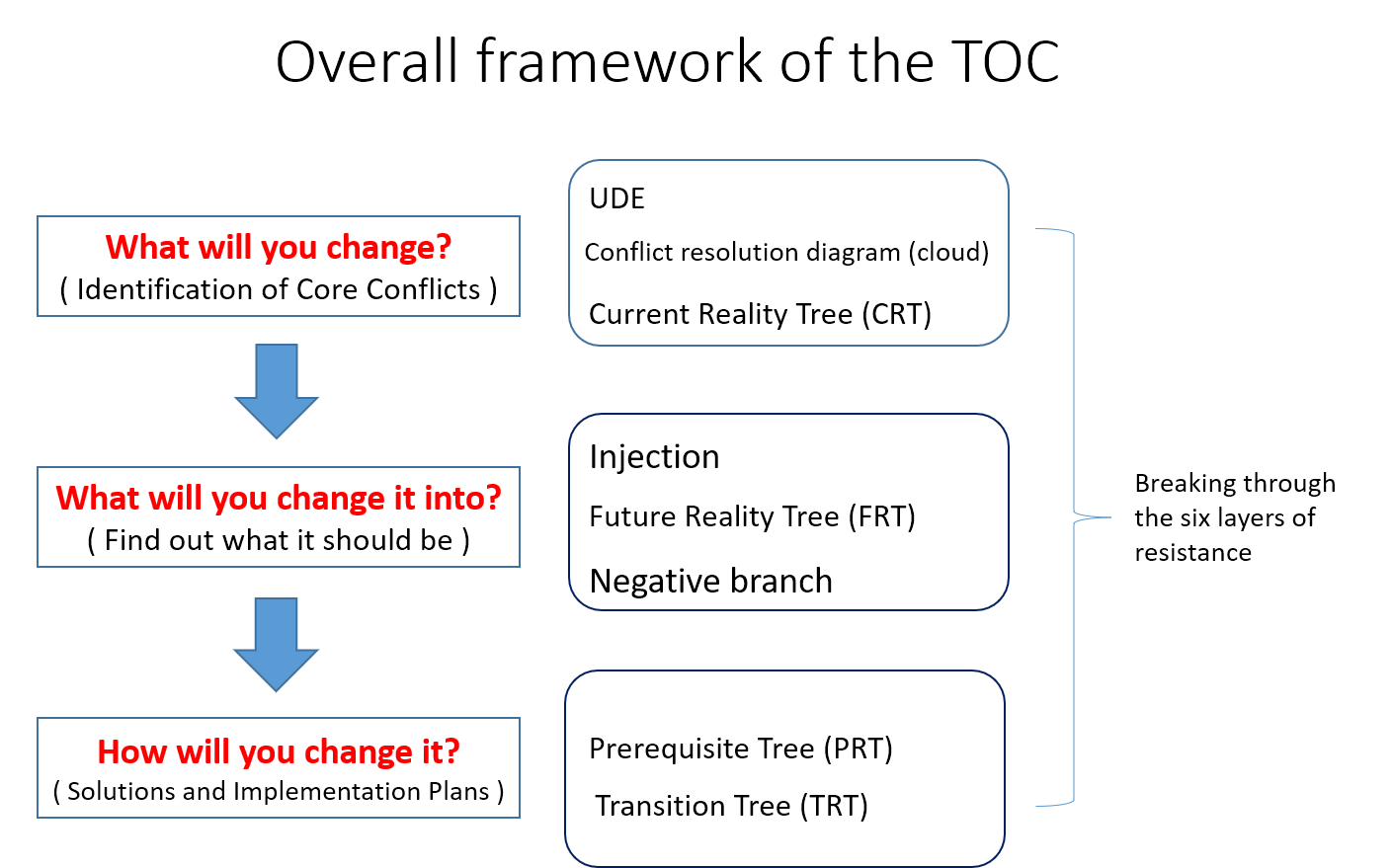
The reason why it is important to follow the three steps is that in non-strategic behavior, when one problem arises, a solution is immediately thought of and implemented.
Solutions derived without identifying the problem and setting a goal are often ad hoc or cop-outs that do not solve the underlying problem.
The very idea of TOC is strategic action itself, and I believe that strategic planning and TOC are very compatible.
Reference article:
Structuring Problems in Development Organizations(Part 1-5)
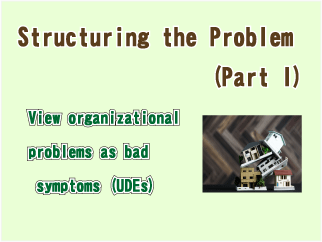
The process of creating a future tree from the current state tree using the TOC process for common organizational problems in development organizations will be explained.
Applying TOC to Product Development
TOC originally started as a scheduling system for production plants, became an improvement framework for production plants, and further evolved into an improvement system for various corporate issues.
Following his first book, “The Goal,” Dr. Goldratt published “The Goal 2“, Change the Rules“, “The Critical Chain” and, “The Choice” to show how TOC can be used outside of production.
In “The Goal 2” TOC is used to revitalize three companies by turning around their businesses or changing their business models.
In “Change the Rules” we show that IT implementation alone will not increase a company’s profitability, but that changing the rules can increase the throughput of the system.
“Critical Chain” puts the concept of TOC into so-called project management and proposes a project management method called CCPM.
“The Choice” shows us the prerequisites of TOC, such as “things are simple” and “there is always a win-win solution,” through examples and a dialogue between a father and his daughter.
Reference article:
We have been working with our clients to use TOC to solve problems in product development organizations.
In the course of these activities, we have learned that there is a certain degree of commonality among the issues faced by product development organizations.
We have explained in a separate article, “Structuring Problems in Development Organizations, “Structuring Problems in Development Organizations,” how to decipher these commonalities and structure the problems (what to change).
The TOC approach can of course be applied to product development, but it can also be used in many other situations.
When you get into the habit of pursuing not only the superficial events of a problem that is occurring, but also the essential things that are difficult to see, you will be able to deal with any problem successfully.
Goal Setting for Product Development Organization Improvement
TOC is a method aimed at increasing the overall throughput of an enterprise system.
It also states that the purpose of a company is to continue to make money.
Therefore, even in improving the product development organization, it will be meaningless unless it ultimately leads to the company’s profit.
Of course, the product development organization alone is not solely responsible for making profits, and there are many points of improvement that can be made to increase profits.
In improving the product development organization through TOC, the goal of the product development organization can be “to increase profits,” but I think it is also effective to raise a secondary goal, which is “to increase profits.
For example, it could be “to continuously develop products that deliver new value to customers,” “to release products in half the time of competitors,” or “to consistently release products that cost 30% less than competitors.
In terms of the TOC process, the bad phenomena that are happening are connected by causal relationships, and the major source of the causal relationships is likely to be the root cause, and the key problem at the end of the causal results may be the event you most want to solve, i.e., the goal.
In other words, in the TOC process, the goal is the world that will be created by making all current problems better (the future tree), and if we consider whether what is expressed in this future tree will lead to increased profits for the company, it will match what the company top management wants to do.
The TOC framework becomes very easy to understand when it is superimposed on a company’s management and development strategies.
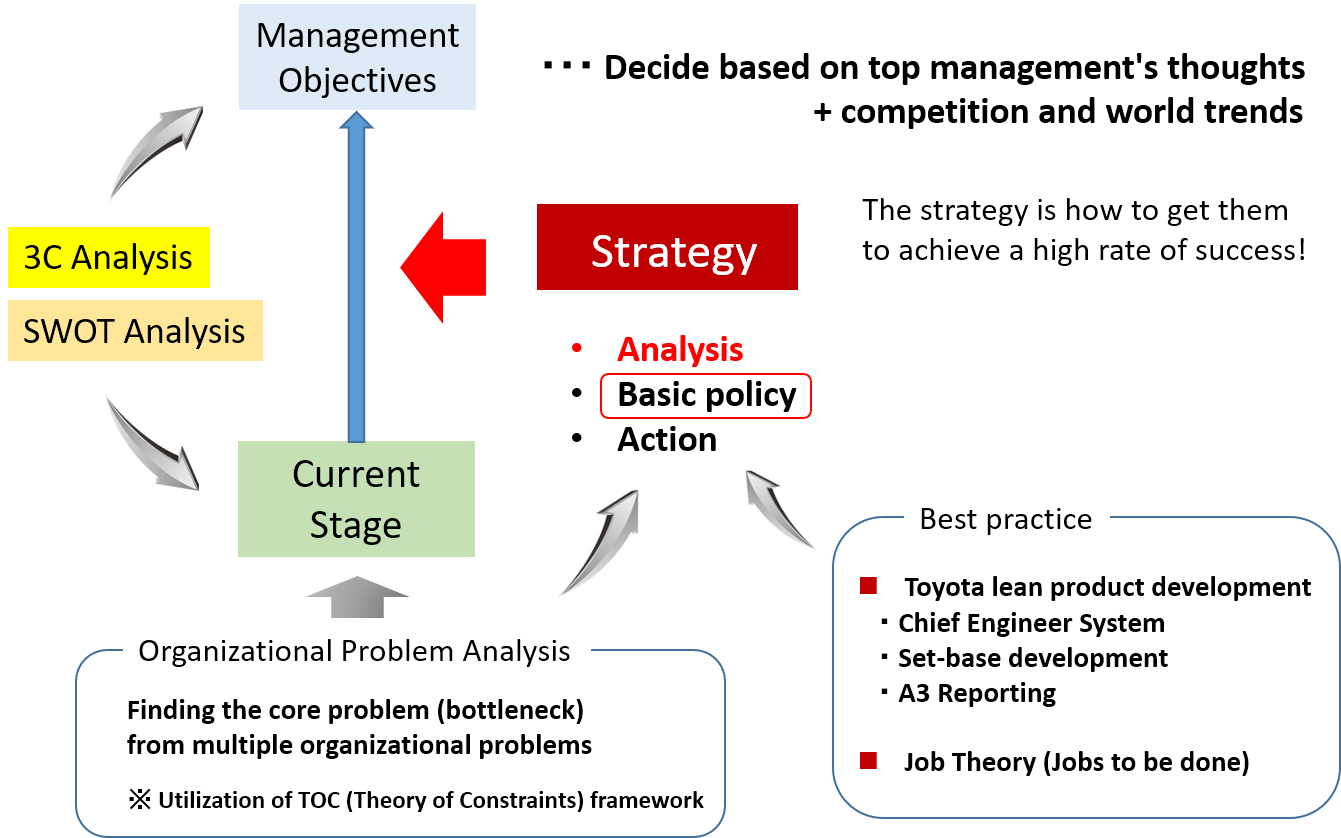
The diagram above shows a framework that merges the TOC framework with strategic thinking methods using 3C, SWOT analysis, etc., and takes cues from Lean product development methods and job theory as best practices in deriving basic strategic direction.
By setting goals that are connected to management goals, i.e., top management’s goals, and ultimately, to continue to make money, the improvement will focus on overall throughput.
Problems Specific to Product Development Organizations
Here are some examples of problems that commonly exist in product development organizations.
- A lot of time is taken up with miscellaneous tasks
- Unclear who is responsible
- High rework rates
- Failure is denounced
- Similar failures are repeated
- Fewer engineers understand the product as a whole
- Young employee turnover is increasing
- New concept products have not been created for a long time
- Veteran’s knowledge and know-how do not remain in the company
- Not knowing what others are doing or what is going on
- Schedule delays have become the norm
- Lack of independent prototyping and proposal of ideas
- Young people do not realize the growth of their technical skills
- Know-how is not documented
- Failure to understand the real issues and potential needs of customers
What do you think?
This is only an example, but it is an unfavorable situation (UDE) common to many companies I have had the pleasure of working with.
These bad situations in product development organizations, or UDEs, from which we seek organizational bottlenecks, are described in another series of articles, “Structuring Problems in Development Organizations” ((Part 1-5)”.
In conclusion, the core cloud shown in the figure below is derived, and the hypothesis that this is the bottleneck of the organization is established.
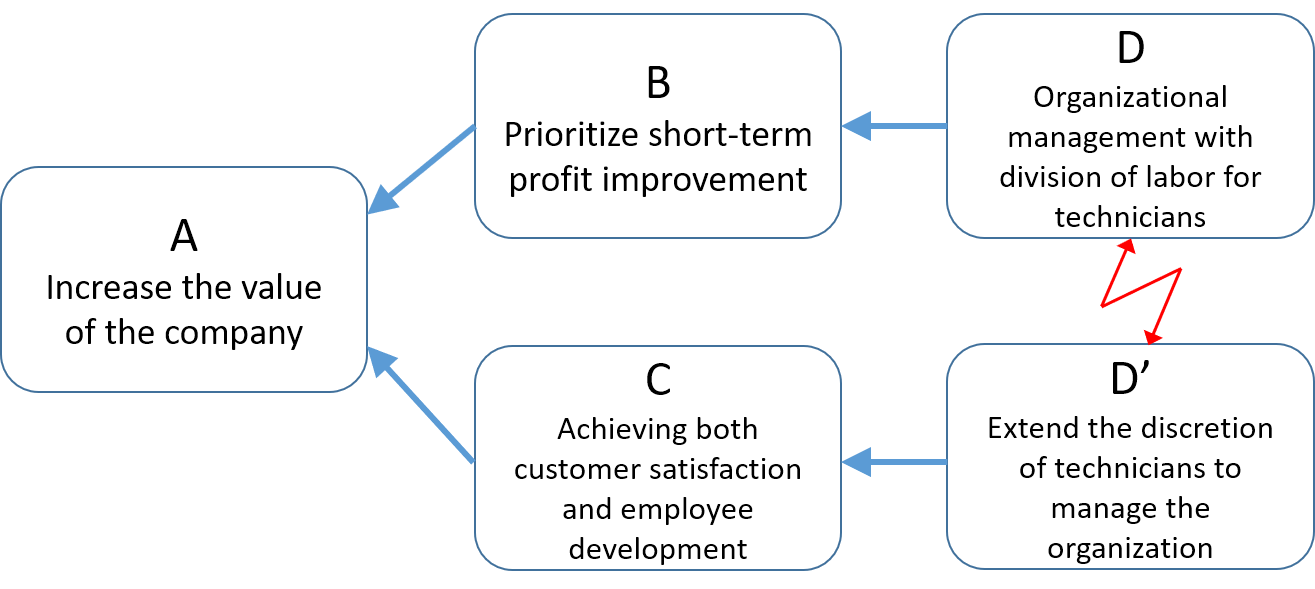
Our recommended strategic approach is to utilize lean product development methods and job theory as clues as to how to solve this core cloud.
This is not to imitate the methods as they are, but rather to grasp the essence of the problem and incorporate the essential significance of best practices as a solution.
Reform Support for Product Development Organizations
We provide consulting services specializing in product development innovation.
When reforming a product development organization, we take the approach of first recognizing the current situation and setting goals with the client company, and then creating a reform plan.
We are also certified by Jonah in TOC, so we are able to practice TOC, but we also have partnerships with several TOC professionals outside of our company, which enables us to provide optimal solutions to our clients through collaboration between product development innovation consultants and TOC consultants, as needed.
As for human resource development, learning the TOC thinking process can help employees develop their logical thinking and enhance their individual and organizational problem-solving abilities.
First, please contact us to discuss your concerns.