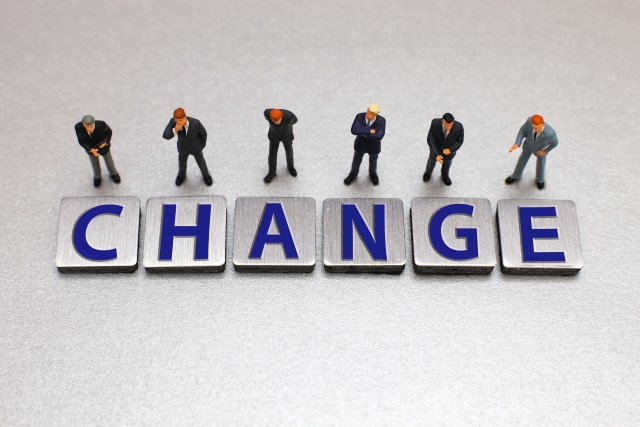
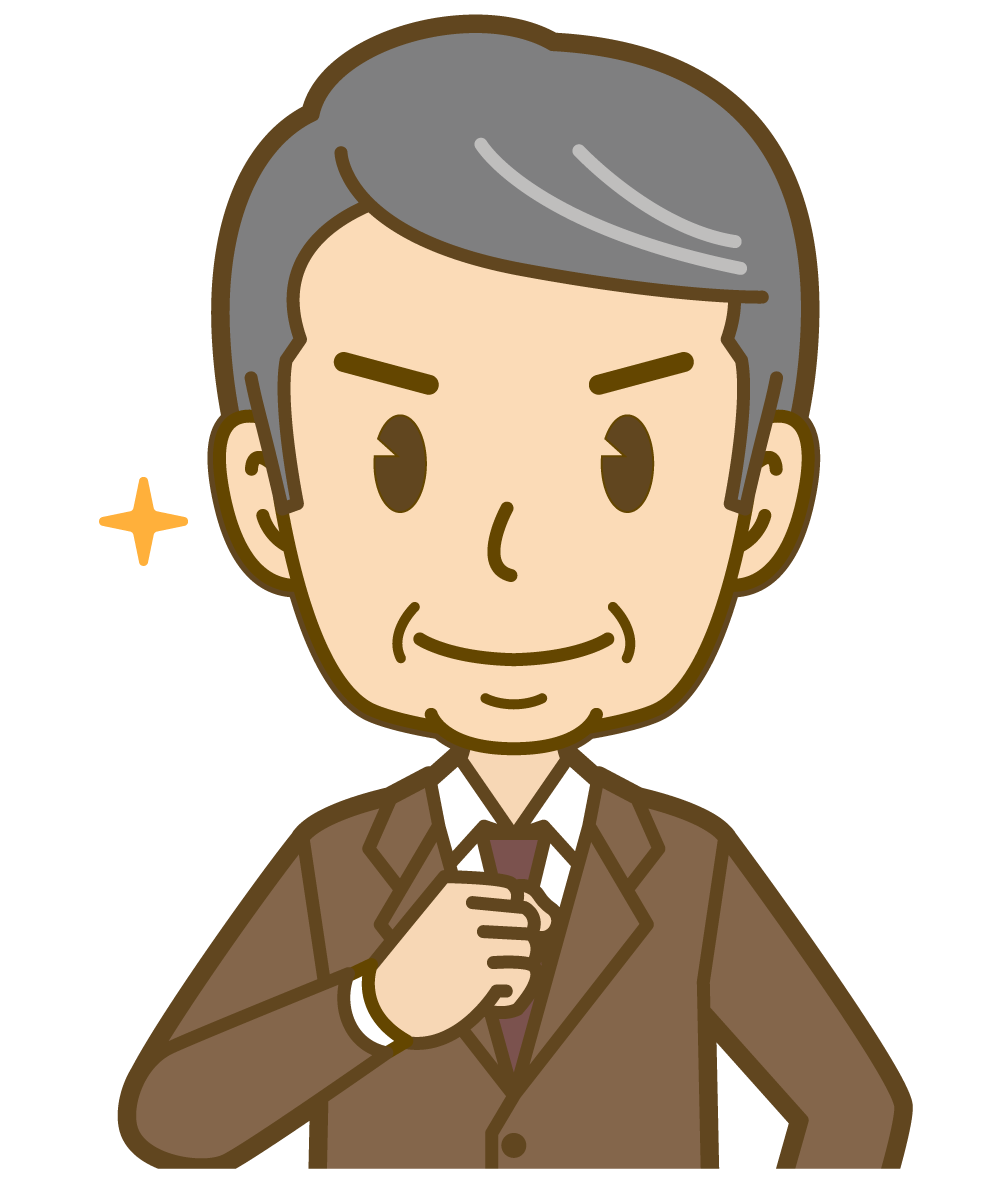
The right way to reform a product development organization is to create your own development system, not just bring in examples from Toyota and other companies!
While we recommend and encourage the implementation of Toyota’s Lean product development methodology, it is not possible for a non-Toyota company to implement the Toyota form as-is. Unless you learn the essence of the development system and organizational capabilities from Toyota’s method and create your own development system and organizational functions to suit your company’s characteristics, you will not succeed in organizational reform.
Organizational reform will always fail if you try to adopt only the form of Toyota or any other company’s best practices!!
As a consultant specializing in product development, I will provide you with the essence of Toyota’s Lean Development Methodology, and show you how to objectively understand your company’s issues, set goals to achieve, and realize organizational and process reforms unique to your company through a strategic approach based on the gap between the current situation and the goals.
Contents of this article
-
- Mistake of trying to incorporate other companies’ case studies in a formality
- Reform is to maintain efficiency and regain what has been lost
- Achieving results one step at a time; time is needed to achieve major results
- A strategic approach is absolutely necessary for successful reform
- Create a lot of positive loops and turn it into a strong organization over time
- Increasing the ability of engineers to think through positive loops will increase organizational capacity
- Futureship’s product development innovation support will make your innovation successful
-
- We can provide full management support for your development innovation projects
- We know the essence of organizational problems
- We are the only company that can create a reform plan with a strategic approach
- We have a deep and objective understanding of the best practices of Toyota and other companies in the world
- It is difficult to analyze your company by yourself
-
The mistake of trying to adopt other companies’ case studies in their entirety

I have helped many companies reform their development organizations, and I have found that many companies make a mistake when they start reforming.
They try to bring in the best practices of other companies, such as Toyota’s Lean product development method.
Japanese companies are obsessed with case studies and achievements
Having worked in the U.S. for about 10 years, one of the major differences between Japanese and Western companies is that Japanese companies tend to be extremely concerned about their achievements and case studies.
When a supplier comes to introduce a new product or solution, many Japanese companies ask, “Does that have been proven elsewhere?”
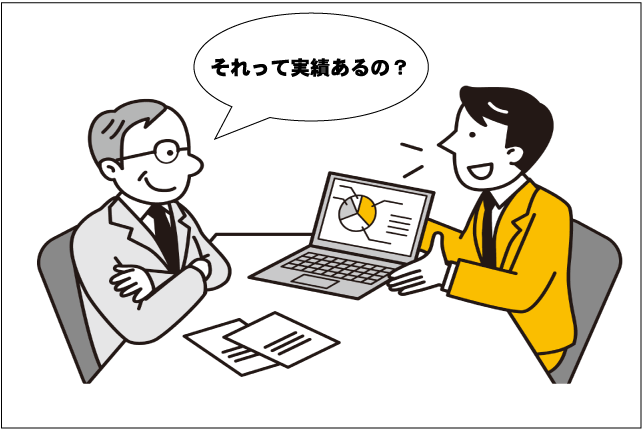
I think we don’t want to be the first to adopt it because of the risks involved.
When I talk about the theory of Lean development at seminars, people ask me
“Can you give me more examples of successes and failures?” Or
or “Do you have any case studies in industries similar to ours? Or
“If you have more examples, it will be easier for me to visualize how to implement it.
If there are more examples, it will be easier for me to visualize how to implement it.
On the other hand, in Western companies, when I introduce a new solution,
You haven’t talked to anyone but us, have you? Why don’t you partner with us only?
This is a response that is almost impossible in Japanese companies.
In other words, Western companies are always aware of the competition and tend to pursue their own unique and original products.
I think that the tendency of Japanese companies to want to hear many examples from Western companies is a direct result of “their desire to imitate”, or “adopt the same form as it is”. “This is not necessarily true for all companies. It’s just a trend.”
It’s not a nice thing to say, but I think that Japanese companies tend to feel secure in being aligned with others, and hesitate to be different.
Do you see similar bad symptoms happening in your product development organization!
Another reason why it is tempting to mimic the organizational structure and development process is that many product development organizations are actually in a similar situation.
What problems or bad symptoms do you see every day in your organization?
If you take a look at the diagram below, you will see that many companies will reply, “Most of what is written here is true in our company.

Of course, there may be companies and organizations that have developed their own organizational culture and have few problems in product development.
However, it is also true that there are so many companies that are suffering from the same symptoms.
Then, I believe that the reason why different companies started to suffer from the same problems is due to the historical background of the development of the manufacturing industry in Japan.
Reference article: “Structuring Problems in Development Organizations”
What I’ve prioritized and what I’ve sacrificed in the process of growing up
Young people may be put off by this talk of the past, but in the 1970s and 1980s, Japanese companies dominated the world with cheap, high-quality products, and books such as Japan As No. 1 became bestsellers.
Companies were able to sell their products as long as they made them, and they expanded their profits by expanding their product lineups.
Rather than coming up with a new product, companies would make money by making minor changes to existing products.
For this reason, companies are accelerating the development of minor changes, and in order to do so, they are making a big effort to improve the efficiency of product development.
The division of labor in product development will be promoted, creating specialists in small areas to develop products in a flowing manner, for lack of a better word.
It became possible to develop multiple models at the same time, and as a result, the efficiency of product development was won, and many companies achieved stable growth.
At the same time, however, I believe that the increased efficiency of product development has sacrificed the chance to create new products, and has left behind the ability to nurture the thinking and creativity of individual engineers.
In addition, the extreme division of labor has drastically reduced the number of personnel who have a deep understanding of the entire product and the number of leaders who can oversee the entire project.
This negative effect is not immediately apparent.
In contrast to the efficiency improvements in product development, which immediately contributed to increased profits, the sacrifice of training engineers and leaders has slowly weakened the company over the years.
As the strength of individual engineers wanes, they eventually become middle managers and lead the organization, which in turn weakens the organizational capacity.
In this way, I believe that over a long period of time, the organizational problems mentioned above have become apparent, and many companies have developed the same bad symptoms.
The Gap between Top Management’s Thoughts and the Feelings on the Ground
Individuals and organizations have been weakened over a long period of time, but I don’t think we should think that anyone was at fault for this.
As a top manager, it is not wrong to aim for efficiency in product development, and the company has actually grown by doing so.
However, it might have been possible to notice the negative effects of increased efficiency at some point and take action to deal with them.
In any case, it is essential to rethink that the efficiency improvement that the top management aims for and the wishes of the front-line workers are issues that must be balanced.
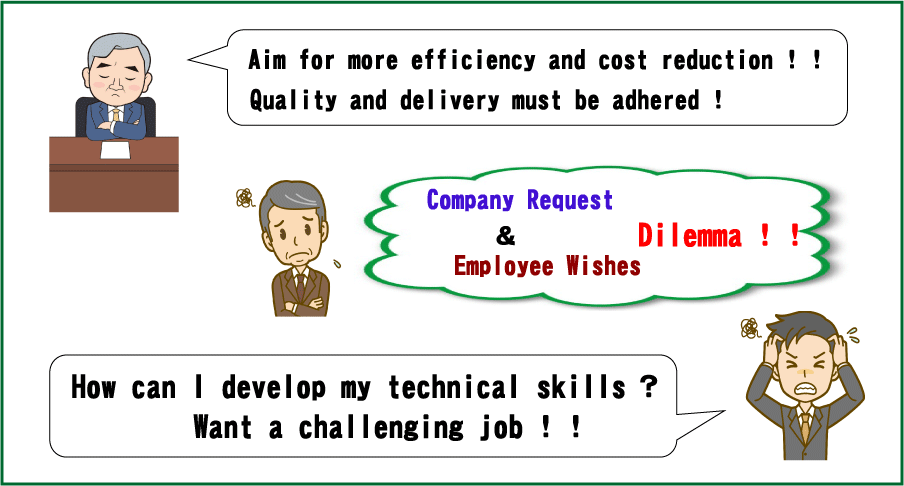
Reform is about maintaining efficiency and regaining what has been lost
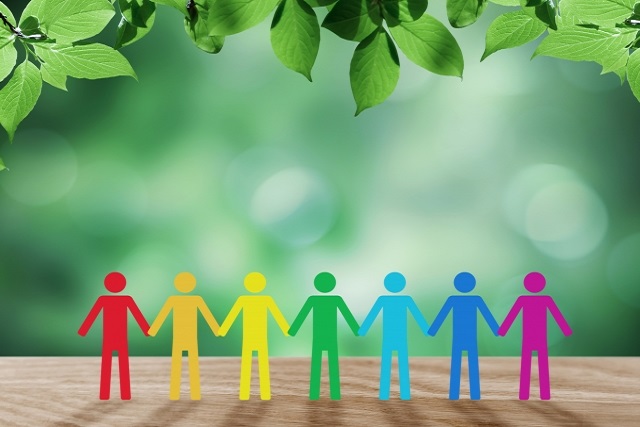
Product development innovation and development organization reform should not negate the history of the company.
It is about retaining what has worked well in the company’s history, regaining what has been lost, replenishing what is missing, and allowing the company to grow significantly again.
A mistake that is easy to make is to leave behind the benefits that have been gained in the history of the company, the importance of “efficiency” in this case, and to proceed with the reform with the main focus on regaining what has been lost.
Originally, it may have been difficult to achieve the two objectives (ex; improving efficiency and training engineers) at the same time. However, both are important to the company.
If you jump to a solution that only acquires what is not done because one of them is not done, you will fail.
Once again, we will consider what we can do to achieve the two important objectives at the
same time.
Building up results one step at a time, but also needing time to reach big results
You may have noticed that in many cases, various problems in a product development organization occur over a long period of time as the company grows.
If this is the case, it means that reform will also take a certain amount of time.
It is understandable that you would want to regain in an instant what you have lost over a long period of time, but let’s think about this calmly.
However, this does not mean that there will be no change or progress in the long time it takes to reform.
Step by step, you will build up small achievements and feel the change and evolution as you aim for the final goal.
A Strategic Approach is Absolutely Necessary for Successful Reform
The various organizational problems that have occurred over the course of history cannot be solved by simply changing the organizational structure.
Unless we grasp the essence of the problem and eradicate the cause, we will not be able to reach the goal we want to achieve.
An approach that only changes the form and organizational structure, relying on the results, will never be successful.
A strategic approach is necessary, but what exactly is a strategic approach?
Although we use the word “strategy” as a matter of course, I believe that there are actually many people who misunderstand it.
A strategic approach is “to understand the high goals and the current situation of your company based on a correct analysis of the situation, and to formulate a simple and surprising policy to close the gap, and to create measures that can be implemented.
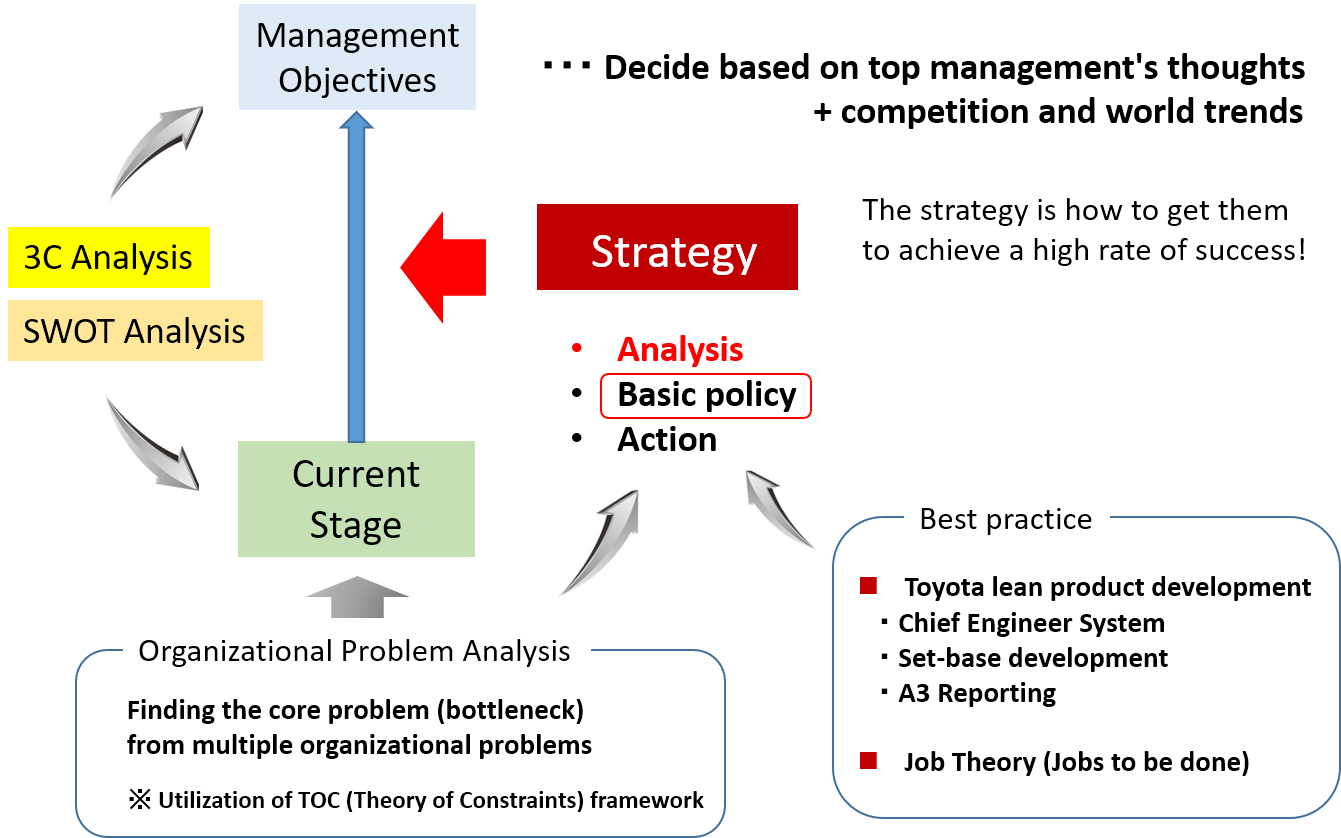
Our strategic approach to product development innovation is based on the framework shown in the figure above.
We focus on what we call correct analysis.
In addition, we use the TOC (Theory of Constraints) thinking process to discover the bottlenecks of organizational problems and attack the bottlenecks in a way that enables us to achieve step-by-step results in a short period of time.
Toyota’s Lean product development method, for example, is based on an in-depth study of how the essence of the method can change individual organizational problems, and leads to strategies.
It is not simply a matter of finding a solution through the method.
By connecting the essence of the method with the solution to the bottleneck of the individual organizational problem, we can implement genuine reform.
Reference article: “Strategic Planning Skills Enhancement Seminar”
Create lots of positive loops to turn your organization into a strong one over time
A positive loop is when, as a result of working on something, other circumstances change, and in turn, the original effort changes positively, and by repeating the process over and over again, the change becomes significant.
For example, in the Lean Product Development Methodology, when practicing the reuse of knowledge in the organization by using the A3 report, this activity will change positively when the following changes occur.
“Write knowledge in A3 report and present it in the organization” → “Share knowledge with each other” → “Exchange opinions on A3 report” → “Become able to write a good report” → “Improve the quality of A3 report” → “Activate knowledge sharing in the company”
When you start any measure, you will not see immediate results at first.
It is important to repeatedly practice and set up a mechanism to make gradual progress in the content.
It is important to set up several such mechanisms and create a system that will increase organizational strength as you continue your daily activities.
Raising engineers’ ability to think through positive loops will enhance organizational capabilities
I believe that the right way to think about development innovation is to set up a positive loop in order to regain the creativity and leadership development of engineers that have been sacrificed by promoting efficiency in product development.
Therefore, it is not possible to innovate by imitating the established organizational structure.
And in order to regain the creativity and thinking ability of engineers, I believe that it is necessary to design a positive loop that is appropriate for each company, based on a thorough analysis of each company’s work methods, the current capabilities of its engineers, and the challenges of its organizational capabilities.
To do this, it is necessary to “know yourself“.
Sun Tzu’s Art of War: “If you know your enemy and know yourself, you will not be in danger in a hundred battles”
This is exactly what I mean by strategic thinking and strategic approach.
Futureship utilizes the TOC (Theory of Constraints) thinking process when pursuing the root cause of current organizational issues.
Reference article: “Using UDE in the TOC thought process to get to the root of the organizational problem”
Futureship ‘s product development innovation support will help you succeed in your innovation
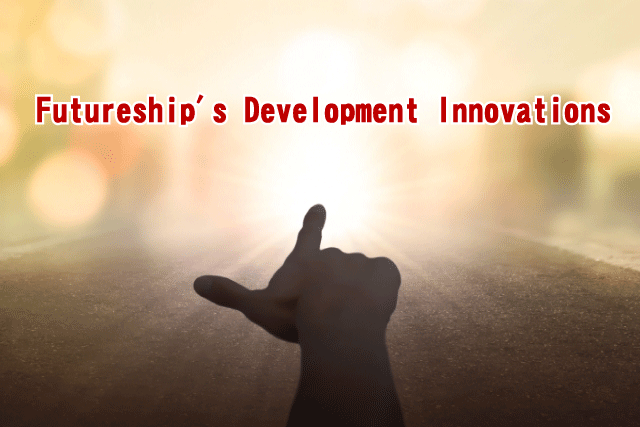
Futureship is not just a consulting firm that teaches methods and theories on development innovation.
Based on our experience in reforming many companies, we know all about the pitfalls involved in reform.
We grasp the essence of each organization’s problems and provide support from the formulation of a feasible reform plan to its implementation.
We can provide full support for the management of development innovation projects
In many cases, you may not have any experience in promoting development innovation as a project.
It is a little different from development project management, and requires experience in driving innovation projects and knowledge of innovation practices.
Please utilize the experience and knowledge of Futureship.
By providing full support to the project leaders, we can not only make the reform itself successful, but also leave the know-how of reform project promotion to your company.
We know the essence of organizational problems
We know the essence of organizational problems in product development organizations, based on our representative’s actual experience in product development in domestic and overseas manufacturing industries, as well as the experience of the many companies we have supported.
He understands the underlying issues of many common problems as organizational dilemmas, and has the ability to simply decipher the intertwined problems from the history of each company.
He is also a user of the TOC (Theory of Constraints) thinking process, and discovers organizational bottlenecks through objective analysis.
We are the only company that can create a reform plan with a strategic approach
There are many consultants who can teach you methods and theories.
There are also consultants who provide frameworks for promoting reform.
However, we are proud to say that we are the only one who can develop a reform plan with a strategic approach that aims at the final goal by deriving the overall picture of the reform and a simple and surprising basic policy from correct analysis, setting up small positive loops and accumulating small results, and then supporting the implementation of the plan until the goal is achieved.
As mentioned at the beginning of this article, our strategic approach also avoids relying on actual results and case studies and trying to adopt only the form.
We have a deep and objective understanding of Toyota and other successful cases in the world
For example, Toyota’s Lean development method may not be as knowledgeable as people from Toyota, but people from Toyota don’t know anything other than Toyota.
So, they may not know how great the Toyota methodology really is.
There are many companies, Toyota and non-Toyota, that are successful in product development.
The important thing is to understand the difference between successful and unsuccessful companies, and to know how to help unsuccessful companies become successful.
I believe that the essential significance of Toyota-style Lean development can only be implemented correctly if you have a deep understanding of your company’s issues and the essential meaning of Lean development.
It is difficult to analyze your own company by yourself
“If you know your enemy and know yourself, you will not be in danger in a hundred battles, “but in fact,” knowing yourself” is surprisingly difficult.
This is because we do not know much about other companies.
Because I have solved problems for many companies, I can help companies analyze themselves accurately from a third-party perspective.
Of course, people inside a company will have more knowledge about the company, but without being able to make comparisons, an accurate analysis cannot be done.
There is also a limit to how much information about the enemy can be gathered by each company.
Based on our experience, we can provide you with information on other companies as long as it does not violate confidentiality.
Let FutureShip, with its experience, help you analyze your enemies and yourself.
If you have any questions about our services, please contact us using the contact form below.