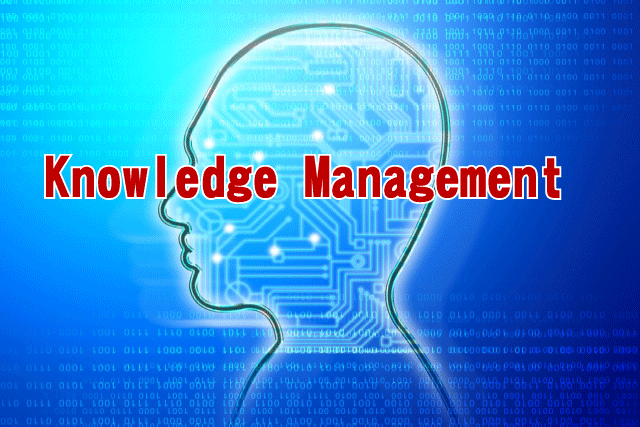
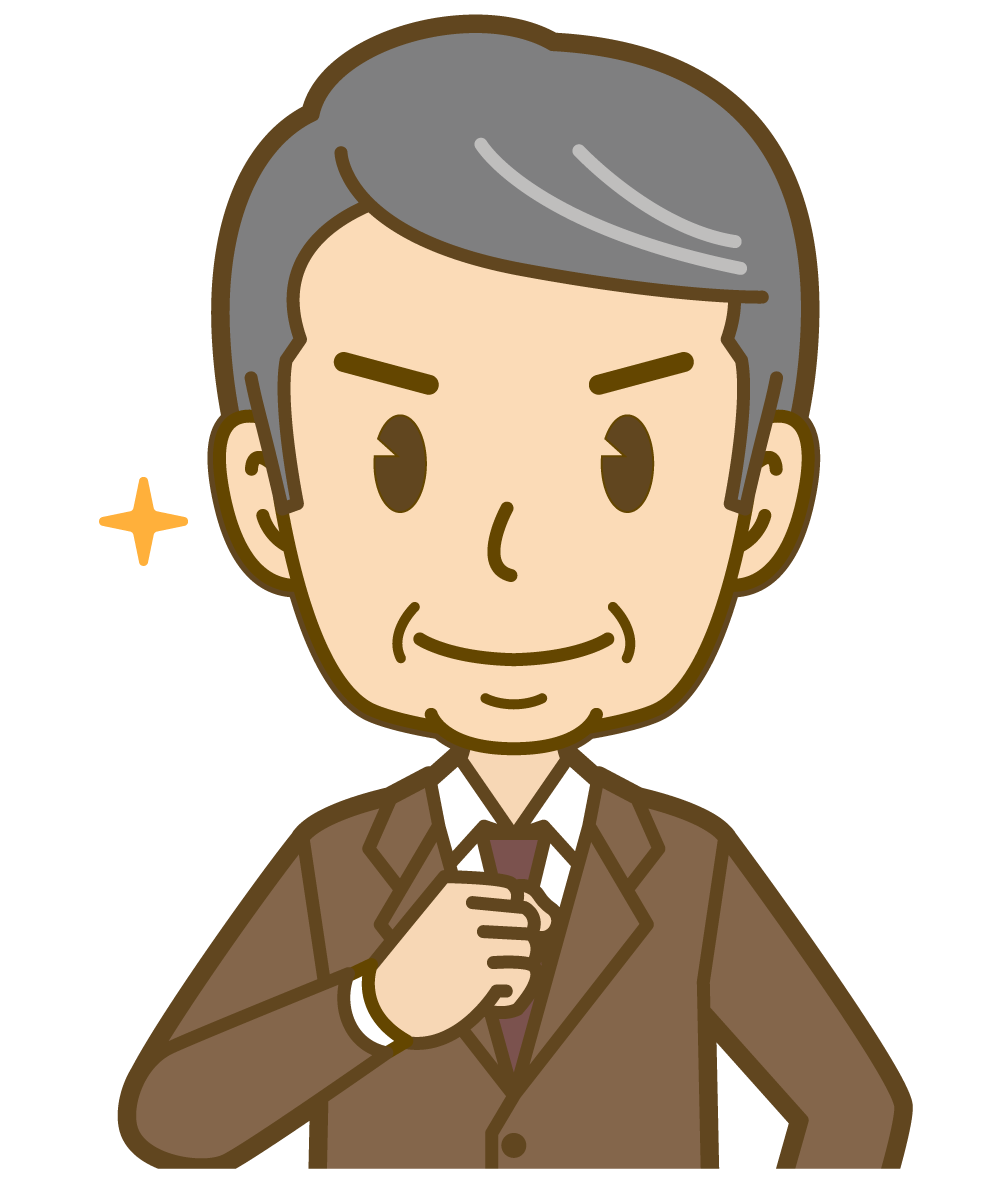
Successful reforms in Toyota-style lean product development integrate knowledge management into the development process!!
Organizational reform in Lean product development will not succeed simply by creating processes and rules such as the Chief Engineer System, set-based development, and A3 reporting. It is most important to complete the knowledge management structure along with the development process and new organizational structure.
The most common cause of failure in implementing Toyota Product Development is trying to adopt only the form of the system and the organizational structure!!
The essence of a development organization that can continue to fight for a long time is to keep generating knowledge and to utilize the generated knowledge carefully and without waste. Just as in lean manufacturing, the goal of lean product development is to create and distribute the necessary knowledge as and when it is needed.
This article
- Incorporating Lean Product Development Components Alone Will Not Achieve Results
- The Most Important Thing in Lean Product Development is the Utilization of Knowledge Assets
- What is lacking in the practice of knowledge management is a conception of the quality of knowledge
- The perfect form of Lean product development is a knowledge management system itself
Merely incorporating the components of Lean product development will not produce results
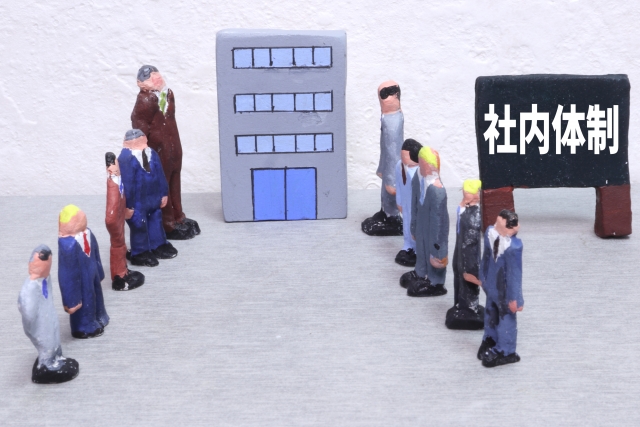
As explained in detail in “What is Toyota Lean Product Development?“, there are three key elements of the Lean product development methodology.
- Chief Engineer System
- set-based development
- A3 Report
The Chief Engineer System is not just about a strong development leader, but about creating an organization that continues to produce hit products through the presence of a charismatic leader who controls the entire value chain spanning planning, development, production, purchasing, sales, and maintenance.
Set-Based Development is a method of proceeding with product development by changing the unknown into the known one by one, while retaining the possibility of multiple methods, rather than deciding on a single method at the product development concept stage. By setting small units for hypothesis testing, product development can be carried out quickly and reliably.
The A3 report is a system that enables the reuse of in-house knowledge by condensing all the contents into a single sheet of A3 format and concisely communicating what is necessary for the reader.
Each of the contents can be viewed as an independent methodology or theory.
And what many people feel after learning about lean product development methods is that it seems difficult to incorporate all of them.
In particular, everyone feels that training a superman like a chief engineer does not happen overnight, but that seems to be the reason why they do not try.
Also, set-based development requires a major change from the current way of doing things, and it has to be promoted company-wide, and we often hear people say that they are not sure how many people will support it.
Although it is not a process of elimination, there are actually many cases where the idea is to first create an A3 report culture, thinking that A3 reports may be relatively easy to introduce.
This approach, that is, the idea of starting with the use of A3 reports, is not wrong in itself, but there are cases, however, where companies proceed without discussing why they are doing A3 reports and what kind of changes they expect from the introduction of A3 reports, resulting in a situation where the A3 reports do not produce results and disappear spontaneously. As a result, it is sad to see the situation disappear without any results.
While it is true that the three key elements of chief engineering, set-based development, and the A3 report each have deep significance, they do not all have to be in place.
Rather than trying to get them all in shape, I would like to see you draw from the theory of Lean Product Development to find out what is wrong with your company’s current situation and to get ideas on how to solve it.
Now, let’s look at how to improve your product development organization and processes by drawing ideas from the Lean product development methodology.
The most important aspect of Lean product development is the utilization of knowledge assets
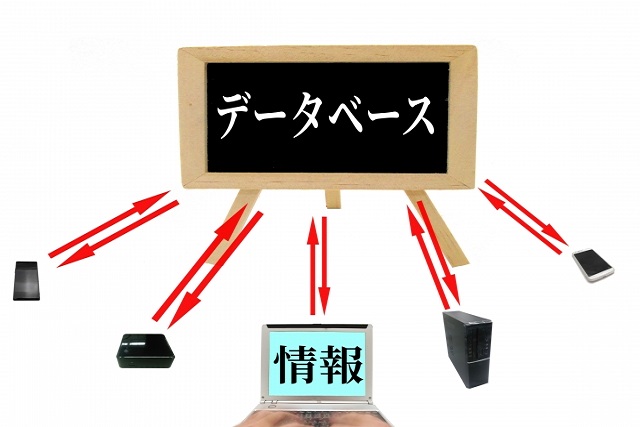
We believe that the key to Lean product development methodology is the utilization of “knowledge assets”.
What knowledge does your company not have?
What effective knowledge does the company have?
After being well aware of the fact that
Acquire “knowledge” you do not have by learning.
The “knowledge” that we have will be effectively utilized within the company.
The ultimate form of a product development organization is to complete such a system.
pitfalls associated with knowledge
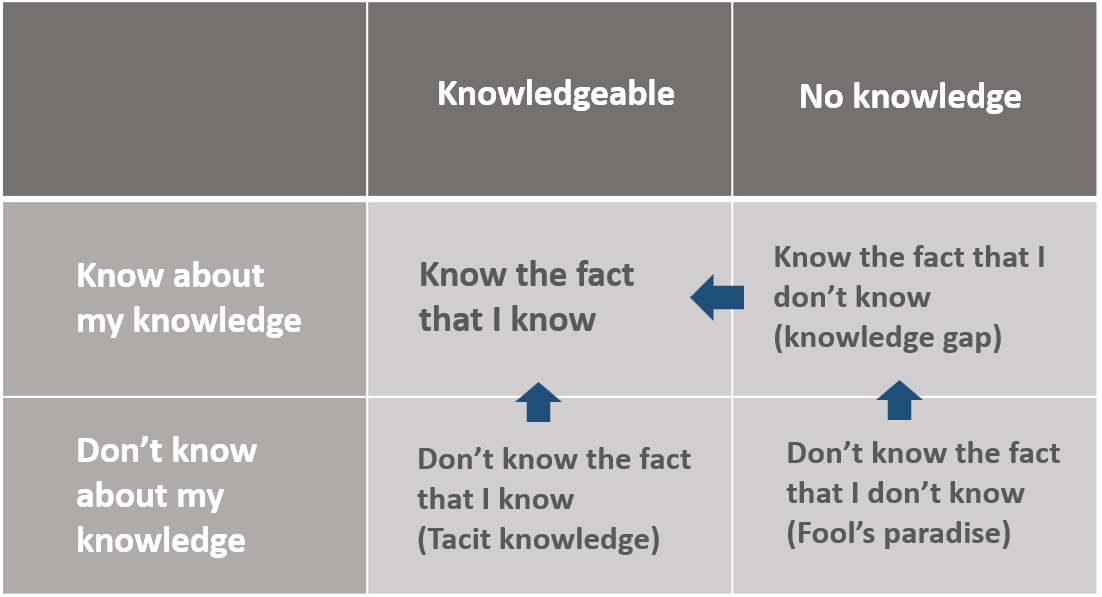
It is very common that you know that you are “knowledgeable” about something.
If you know that you are “not knowledgeable” about something, that is a knowledge gap, and if you acquire knowledge, it becomes new knowledge.
In other words, you can change “not knowing” into “knowing what you know,” and this activity is learning, or in the case of a development organization, it is an act of development.
However, human knowledge is limited, and the knowledge that exists in the world is also infinite.
Therefore, there are actually many things that we do not even know that we do not know.
It can be said that realizing this “not knowing what we do not know” and changing it to “knowing what we do not know” is also learning.
In a sense, discovering the “unknown” and turning it into a challenge is also an act of development.
And there is one more important thing about knowledge. It is not realizing that you have knowledge.
To put it a little more simply, we think, “That’s just common sense,” and we don’t think that we ourselves have knowledge that others don’t have.
This is called “tacit knowledge” or “knowledge bias.
In the corporate world, many companies have seen veteran employees leave the company without passing on their know-how to their juniors, saying, “I don’t need to explain it to you,” resulting in the disappearance of knowledge from the company.
This is a very dangerous thing to leave “knowledge” to individuals.
In many cases, the knowledge in a company is transferred to the individual.
This in itself is unavoidable in a sense, but what should be done is to transform the knowledge acquired by each individual into a company’s asset and to activate corporate activities.
Transforms a generative process into a non-personnel system
In corporate activities, the abilities of each individual are extremely important.
It is considered effective to raise the overall level of individual capabilities in order to enhance organizational strength.
However, an extremely gerrymandered system will not result in stable and continuous organizational strength.
To create a strong organization that can compete over a long period of time like Toyota, it is necessary to create a system that does not rely on strong individuals, but rather brings together the knowledge assets within the company to create a system that is not a genus.
The Lean Product Development System is for this non-personnel development system.
First, take inventory of what the root of your company’s problems are.
Try to identify where the important know-how and knowledge in your company resides.
Are the organizations within the enterprise being leveraged and used as a foundation for the next innovation?
Are failures shared and systems in place to prevent the same mistakes from happening again?
Why do quality problems occur repeatedly?
Why does it take so long to solve quality problems?
If you trace back to the source, you will find that “knowledge” is not being treated with care as a company asset.
What is missing in the practice of knowledge management is a conception of the quality of knowledge

As companies realize the importance of “knowledge,” there is a call to strengthen knowledge management.
This is very important, but what does knowledge management mean?
In a sense, words are very irresponsible, and many people can imagine what they mean by the term “knowledge management.
And then, they proceed to talk about what they have imagined without confirming whether their ideas are in agreement with each other.
From my experience, many people seem to think that knowledge management simply means organizing reports and other documents so that those who want them can search and retrieve past information.
I feel that many companies, especially with IT in mind, tend to place more emphasis on searching.
In other words, many people’s idea of knowledge management is to first consider already existing internal information as knowledge, and then to create a system that enables the utilization of past knowledge.
Do you really think this is a good idea?
I would like to point out two things here.
- Is the information we have now usable information?
- Is the information we have now the information the company needs in the future?
If the information is not usable, it will not be utilized
In order to make use of the knowledge, the knowledge must remain as document information.
In other words, whether the knowledge is usable or not depends on the quality of the document information, or in other words, the quality of the report.
I believe that how to improve the quality of reports and maintain that level of quality is actually directly related to the company’s organizational strength.
The A3 report of Toyota’s lean product development is one of the reasons for Toyota’s strength, not simply because the report is in the A3 format, but the most important thing is that the quality of the report is enhanced and maintained through the A3 report format.
Now, let’s look at what a usable report looks like, disregarding the substance of the report, and looking at the conditions for being usable, or in other words, being able to be utilized.
- The contents of the report are accurately and clearly conveyed to the reader
- It does not contain unnecessary information and has a clear storyline
- It should not be all text and should not be resistant to the reader’s resistance
- Something the reader wants, i.e., something that is useful to the reader
- The title and introduction should be sympathetic
- Leads the reader to the right action
In this way, a usable report can be described as one that is written with the reader in mind.
However, it must be said that the reality of many corporate reports is that they are often writer-oriented.
They tend to be written as the writer wants to write them, or as the writer and the supervisor who directly receives the report can understand them.
From the perspective of knowledge management, if a report is to be widely utilized within a company, it must be useful to a wide range of readers and potential readers.
If we create a system for searching without checking the quality of existing reports, we end up with a system that will not be utilized.
It will not be useful unless we pursue what information is required
Another reason why the system will be useless if we only consider the utilization of the information we have is whether the information to be managed is what is required in the first place.
I believe that the most important concept in knowledge management is the idea of treating knowledge, or information, as a commodity.
I believe that a system in which knowledge, or information, is distributed as a product within the company is what knowledge management originally seeks.
Because it is a product, it cannot be sold unless it meets the needs of customers, or readers.
The writer of a report, in other words, an information transmitter, should be able to transmit information that customers (readers) want, in a quality that they can use, so that there will be a market in which many readers will make use of the information.
The concept that is lacking in the knowledge management that many companies are working on is that they do not try to understand what kind of information will be needed in the future within the company, or the needs of the customers (readers) who will use the information.
In other words, they are thinking only about existing reports and how to access them, without getting into the problems of those who create the reports.
In other words, a writer-driven report is a product-out rather than a market-in approach to product development.
Of course, there are many excellent reports among the existing writer-driven reports.
If we can get access to information from them that can be utilized, we may be able to see improvements over the current situation.
However, organizational reform is not a comparison to the status quo.
The purpose of reform is to achieve the goal set for what the organization as a whole wants to achieve.
By leveraging knowledge assets, we can
- Continuous innovation
- Never repeat the same mistake twice
- Change the organization into one that wins over the long term
If you set a goal such as “to achieve the goal,” I think you should also decide how you must utilize “knowledge assets” to achieve the goal.
On the other hand, I think that changing the way reports are written to be reader-driven is actually a very big change.
Organizational culture is something that is created and established over a long period of time.
I think the reason organizational reform is difficult is that it requires changing a culture and mindset that has been established over a long period of time.
However, what is more fundamental is whether or not the organization realizes that a change in culture and awareness is necessary in order to achieve great results.
Reference article: ”Real Knowledge Management Learned from Toyota’s Lean Product Development”
The perfect form of Lean product development is a knowledge management system itself
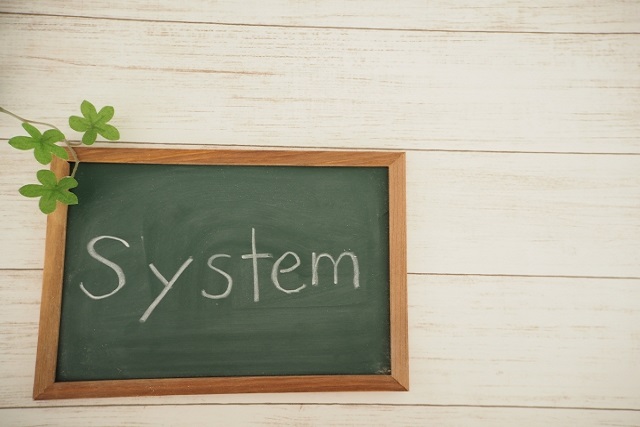
After nearly a decade of practicing Lean product development methodologies, we have come to the conclusion that the ideal product development system is one that builds and operates a real knowledge management system.
By “real,” we mean that there are fakes out there, and many companies have created fake knowledge management systems that have failed.
I believe that the A3 report for Lean product development and set-based development is one way to perfect knowledge management.
You don’t necessarily have to use the A3 format, and that is not a must for the set-based development methodology.
In short, it is about how to acquire knowledge that you do not have, how to maximize the use of the knowledge you do have, and how to create a system to distribute “the necessary knowledge information as and when it is needed”.
Ideal knowledge management system
The goal of practicing Lean Product Development is to create a strong product development organization and product development process that will continue to win over the long term.
Long-term winning organizations are
- Not a generic organization.
- But have high individual competence and motivation
- Continuously growing through knowledge assets
And to grow with knowledge assets, the organization must be able to grow with knowledge assets.
And in order to grow through knowledge assets
- Knowledge is shared in real time within the organization
- Utilize knowledge to learn from “mistakes”.
- New knowledge is created by building on existing knowledge through new challenges.
The organization should be able to do these things naturally.
What stands in the way of building an ideal knowledge management system is the beliefs that infiltrate the organization.
I would like you to start by reviewing the quality of information for the utilization of knowledge information, not just the existing knowledge information, i.e., reports and documents.
In order to improve the quality of information, it is important for those who disseminate information to become customer (reader) oriented and for the entire organization to have an awareness of the need to improve the quality of information.
It is important to note that knowledge management should not be viewed as an information retrieval system.
We can provide advice on the establishment of knowledge management along with an analysis of your company’s situation.
Please contact us.