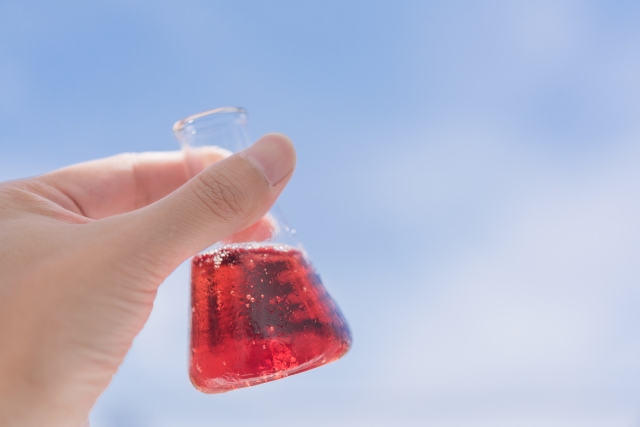
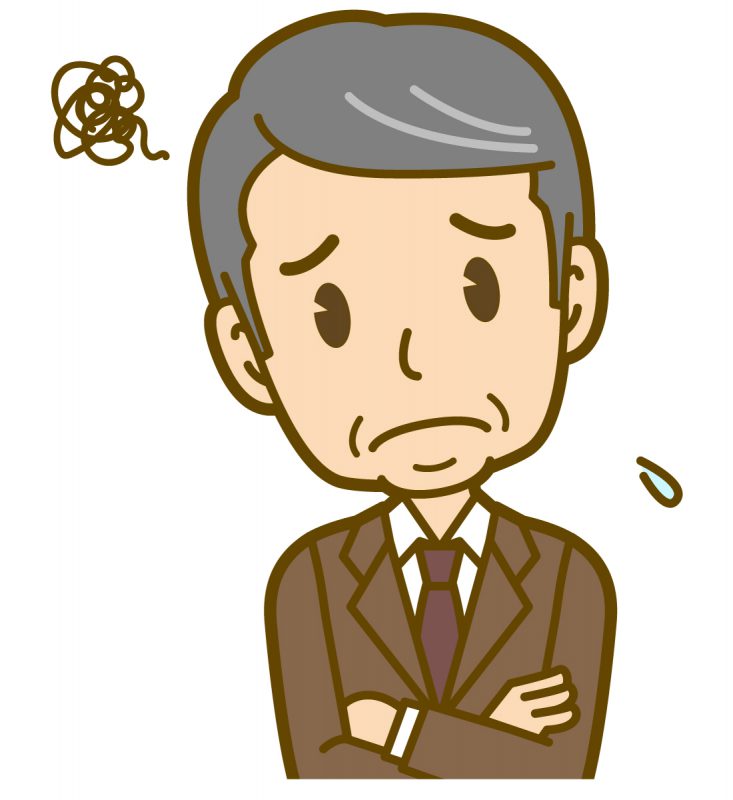
Product Development Organization Exhaustion Out of Control
Engineers in many companies’ product development organizations are exhausted: schedule delays are the norm, 80% of their work is chores, and they don’t feel like their skills are growing. As the problem becomes more complex, we want to at least reduce the turnover rate, but we don’t know how to take concrete steps to do so.
We will answer such questions.
Contents of this article
Three special remedies for motivating development organization
As is often the case with companies that once enjoyed steady growth in their existing businesses, I know many companies that have found it difficult to create new businesses or hit products with new concepts as a result of their focus on improving the efficiency of their existing businesses.
What these companies have in common is a lack of motivation among their engineers.
Each company has different circumstances, so the underlying problems may be somewhat different (although I believe there are many commonalities), but many engineers seem to be physically and mentally exhausted.。
Based on my experience in helping more than 10 companies reform their product development organizations, I would like to focus on the decline in engineers’ motivation and explain three special remedies to stop the condition.
The three special remedies are as follows
- Many engineers take measures to understand the principles of the entire product
- Give each person more than one thing to brag about
- Pay high incentives for quality information dissemination
The following is an explanation of each one.
Many engineers take measures to understand the principles of the entire product
One of the causes of low motivation among engineers is that their skills and status do not improve despite their best efforts
Due to their daily busyness, they do not have much time to study or do what they like to do on their own.
The division of labor in the act of development can also be a cause.
To improve development efficiency in existing businesses, a functional organization can be created for each specialized field, and one specialized field engineer can design the same unit or part for multiple models, so that a similar lineup of models can be developed in parallel.
The throughput of development for the company as a whole will certainly increase, but in essence, it is like a factory line, where one person does only the same work (development) and does repetitive, routine work.
From my practical experience on the factory line, the person in question does not know what part of the whole what he/she is doing and what contribution he/she is making.
If the same thing is done in development, similarly, the engineer gradually blurs what part of the whole he is doing and what contribution it makes.
The overall structure of the product, the principle of operation through the coordination between units, etc. become a world far away from you.
Moreover, after years of doing this, the people around you are said to be experts in something as well, and you can’t find anyone who knows the whole story.
This vicious cycle can lead to a slow investigation of the cause of quality problems, or to many quality problems in cooperation with neighboring units.
The company will also experience an increase in quality problems, the speed at which problems are resolved once they occur will slow down, and the organization will not be able to develop leaders who can grasp the whole picture.
As for the individual, he or she will remain in a state of being a frog in a well for a long time, and will begin to give up on the idea that this is what an engineer’s job is like, and will be buried among the people around him or her.
In my opinion, the biggest bottleneck in the problem of low motivation is the state of engineers who don’t need to know the whole picture.
I believe that the basic measures to tackle this problem are as follows.
Shift to a project system where a small number of people can start up a single model, rather than efficiency gains from a functional organization.
If the cause is that the functional organization is too strong, the functional organization should be stopped and shifted to a project system with a dedicated person for each model.
Some companies are alternating between matrix-type vertical (by model) and horizontal (by function) strength and weakness, etc. However, as the number of models to be developed increases, once the function-based operation is strengthened, the company may run out of personnel when it is time to change back.
Given the circumstances, it is likely that it will be difficult to completely revert back to the original situation all at once, and a gradual shift over time is the most likely scenario.
If the functional organization is to be maintained, the model members should meet in one place during the execution of the model project and be fully vested in the model team.
If the decision must be made to maintain the functional organization, it is to move from a situation where, from the perspective of each engineer, there is always someone around him or her in charge of the same function, to having members who do different functions or the entire model around him or her, so that he or she can naturally understand his or her significance from the perspective of the entire model.
From my experience, this alone will change his/her awareness in a very positive way.
Use about 20% of the total man-hours to have all engineers analyze and report on the overall structure, overall operating principles, etc.
If the decision is made not to change the organizational structure at all, we have to abandon the idea of understanding the whole as on-the-job training, and instead give a place and mission to many engineers to understand the whole using a certain number of man-hours.
Simply studying in a classroom setting does not improve efficiency, so we have them analyze the overall operating principles, including the overall structure and the linkage between units, as a mission.
We recommend using a variety of tools for the analysis.
Some of the tools we recommend and use in lean product development are
-
- Functional structure development diagram・・・Relates functions to unit structure
- Principle of operation diagram・・・Illustrate the relationship between parts, their impact, coordination, side effects and their countermeasures, etc.
- Causal relationship map・・・Illustrates the causal relationship between customer value variables and design variables for each unit.
In particular, the cause-and-effect map will correct the habit of engineers to solve problems only with design variables, discover new technical issues, and understand situations that the organization has no knowledge of.
※*For more information on cause-and-effect maps, please refer to another article, 「Using Cause-and-Effect Maps to Accelerate Product Development Innovation.」
Of the basic measures, the third measure, giving engineers time and missions to analyze using analysis tools and leaving them in a visible form (e.g., reports), may be the most realistic and practical, given that, realistically, organizational structures and processes cannot be changed immediately.
Give each person more than one thing to be proud of.
Even if engineers belong to different functional organizations, it does not necessarily mean that each has a truly strong core competence.
In many cases, they are only currently working on the specialized skills of the department to which they happen to be assigned in the first place, and it is unclear whether it is what they really want to do or what they are best at.
There may be human resource development plans, career plans, and other personnel systems, but these plans are often based on the idea that the engineers themselves do not know how to advance their careers, and simply want to take outside training when and if they want to.
We define each person’s “content” as something that is better than others, that will contribute to society in the future, and that can be used outside the company. We help our clients develop their HR systems by defining how to find the content for themselves and the steps to develop it.
*For more information, please refer to 「7 Steps to Career Development HR System Building Support」
Simply put, this “content” is something that can be taught to others and something that will greatly benefit them by teaching it.
Motivation will increase dramatically once the person starts working toward the “content” because it is directly related to his/her contribution to the company and also increases his/her recognition within the company.
Pay high incentives for quality information dissemination
When discussing development organization issues in many companies, it is often pointed out that there is a poor flow of information within the organization, such as poor communication of information and lack of progress in passing on technology.
When daily work becomes busy, reports are sometimes only addressed to the supervisor to respond to his/her instructions.
We sometimes see cases in which the objectives of accumulating technology, passing on technology, and preserving knowledge in the company are neglected.
Tacit knowledge of veterans, that is, knowledge that is natural to veterans but valuable to the general public, is not passed on to the general public, and if a veteran retires without passing it on, the knowledge is lost from the company.
Young people will stop writing reports because veterans do not leave reports to accumulate and pass on their skills.
Or, even if they do write them, they will be of low quality that will not be communicated to others.
When no one is blamed for not writing reports or for their low quality because problem solving is definitely a higher priority than reporting, this creates a negative spiral and the quality of information circulating within the organization will deteriorate.
It is important to create a culture of writing reports, a culture of promoting technical transfer through reports, and a culture of protecting knowledge assets in the company through reports.
The way to do this is to pay incentives for good reporting or information transfer.
If you make it an obligation, it becomes a burden.
I think it is important to give positive rewards for producing good things.
There are cases where you can do things like include them in personnel evaluations. For example, if you set a quota for the number of reports and evaluate achievement, you will end up with a large number of low-quality reports.
If a system is created in which reports are circulated or posted for the general public to give positive scores to those that are good, and if the number of positive scores is high, the personnel evaluation is moved to the positive side, the general public will get into the habit of looking over reports, and many reports will be created with a strong awareness that they will be read. This should be a good thing.
Various books have described Toyota as having a reporting culture in which everything is written out on A3 paper.
There are a number of companies that are promoting organizational reform using A3 reports, and I think this is a method that can easily produce results because the progress being made is visible.
The method of incentive payment may need to be devised, but I believe that incentives based on positive thinking will improve the motivation of the organization.
Specifics of Organizational Reform
We have looked at the problem of development organizations, focusing on the perspective of low motivation among engineers.
Three special remedies to increase motivation in an organization
-
-
- Put measures in place to ensure that many engineers understand the principles of the overall product
- Give each person more than one thing to be proud of
- Pay high incentives for quality information dissemination
-
Each of these measures is not that difficult to implement.
However, in order to promote organizational reform as targeted, it is necessary to strike a good balance between reforming the awareness of engineers and employees and reforming the organization’s structure, processes, and mechanisms at the same time.
In particular, awareness reform will not only take time unless it is carried out in accordance with a solid policy, but it may also be frustrated in the process.
One way to do this is to get all employees committed to one known method or way of thinking.
We should remember that in the 1970s and 1980s, many Japanese companies treated TQC, a quality control method, as if it were a religion throughout the company, and this led to Japan’s domination of the world with high-quality products.
Rather than the merits or demerits of the method itself, TQC was a company-wide, top-down reform that was carried out without anyone doubting, right down to the end of the line.
Improvement activities such as QC circles, which happen spontaneously from the end of the company, must have contributed greatly to the leap forward of each company.
For our company, for example
-
-
- Toyota-style lean product development methods
- TOC (Theory of Constraints)
-
We are familiar with specific ways to proceed to solve the theme of this issue, which is to motivate the development organization, and other organizational issues by using either of the two as a banner for organizational reform in the company.
We will propose an appropriate way to proceed depending on the situation of each company.
Please contact us using the form below and we will get in touch with you. Please contact us to discuss your organizational issues. We will propose a specific way to proceed with organizational reform.