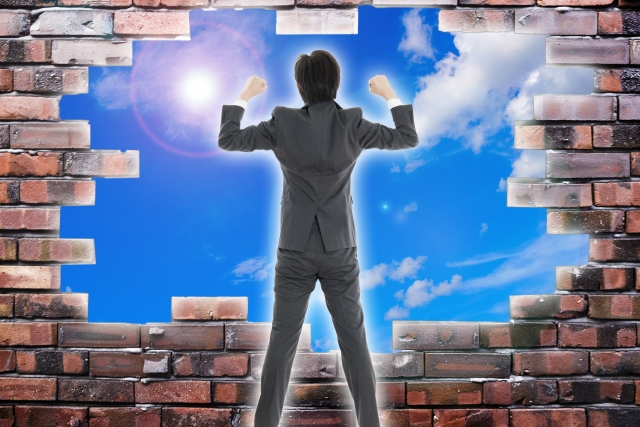
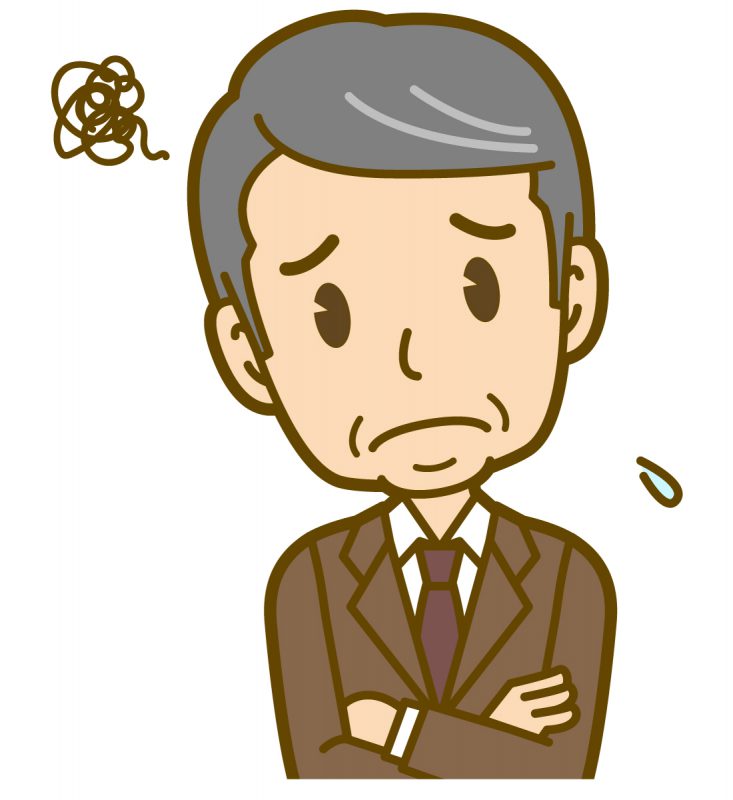
I understand the concept of set-based development, but isn’t it difficult to put it into practice?!
After reading the article “Understanding Set-Based Development” I understand the concept of set-base in Toyota-style lean development, but considering the reality of the development process, I am concerned about whether I can really put it into practice because it would require quite drastic changes. I would like to know what obstacles there are and how we can overcome them.
I will talk about the obstacles to implementing set-based development and how to deal with them, based on my experience of realizing reforms through lean development in multiple product development sites, despite setbacks and organizational resistance.
First of all, there are some misconceptions that arise when trying to implement set-based development. Without letting the misunderstandings go unchecked, I would like you to understand the essential significance of the method, clarify what you want to accomplish as an organization in the first place, and proceed with the reform without wavering after confirming that the goals and the significance of the set base for achieving the goals match.
The most important thing, I think, is to create a culture that seeks to release better products to the world based on the “knowledge” and “know-how” that the organization possesses.
In order to achieve this, I think it is important to create a system and a way of thinking that allows information on “knowledge” and “know-how” to circulate like blood within the organization, and on top of that, to create a process of set-based development as a way to proceed with development.
The following is a detailed explanation of the impediments and how to deal with them.
Contents of this article
- A review of set-based development
- Misconceptions and obstacles that hinder the practice of set-based development
- Isn’t the end result to separate element development from product development? Misconceptions about set-based development
- The misconception that it will take more time and cost than before
- Doubt that small experiments are difficult
- Objection that it is not consistent with existing processes
- If the top management can’t make a decision, the reform can’t get off the ground
- How to logically persuade the top management to proceed with set-based development
- Show the objectivity and credibility of the current situation analysis with data and logic
- Understand the top management’s thoughts and the key issues they want to achieve
- Propose a story to solve the top management’s key issues
- Provide concrete examples of successful best practices (set-based development)
- Carefully analyze the side effects, obstacles, and risks of the proposed measures and specify countermeasures
- Summery
A review of set-based development
For more information on set-based development, please refer to the separate article below.
Let’s review it very briefly here.
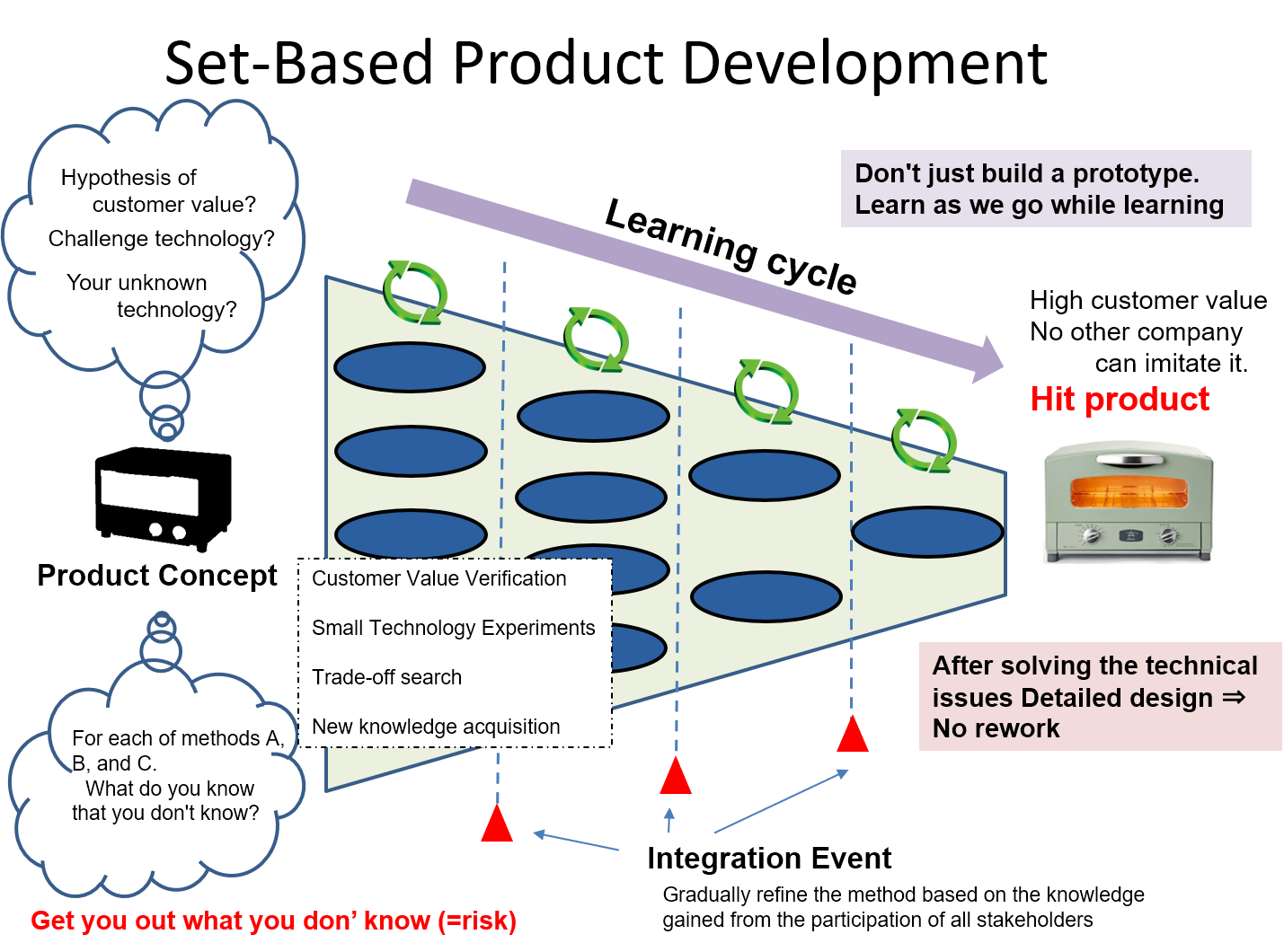
In set-based development, we do not decide on a single method at the product conception stage.
This is because we believe that we lack the knowledge to decide on a method, including the knowledge about customer value.
At the product conceptualization stage, we summarize what we don’t know, what we need to challenge, the hypothesis of customer value, trade-offs, etc., identify all the risks, and then narrow down the method with the agreement of all the stakeholders by eliminating them one by one in the learning cycle.
By repeating the learning cycle, the level of technical perfection will naturally increase, and by the time the method is decided, the technical issues will have been eliminated, and a product that customers really want will have been created
Capturing the essence of Toyota’s lean product development methodology
Aiming for reform through the motivation of young engineers, and
and to reform the company through the motivation of young engineers.
The film depicts the challenge of organizational reform with a unique worldview that is not an imitation of Toyota’s.
For more information, see “Breaking the Rules of Product Development Organizations!” Publication Information.
Misconceptions and obstacles that hinder the practice of set-based development
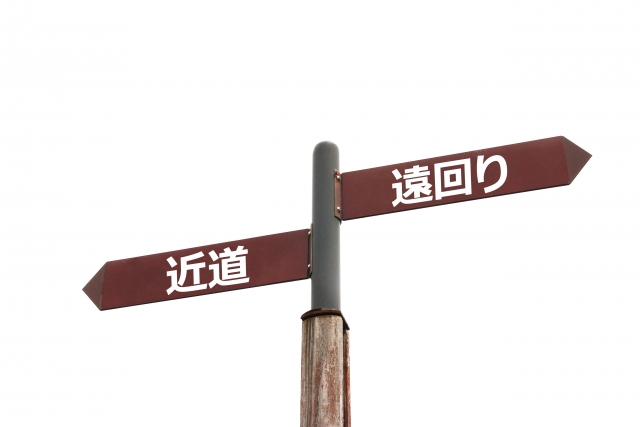
Isn’t the end result to separate element development from product development? The Misconception
The most common misconception about set-based development is, “Doesn’t it mean that you have to separate element development from product development? The most common misconception about set-based development is, “Doesn’t it mean that we should separate element development from product development?
The learning cycle in set-based development is based on the assumption that there are still unsolved problems and risks in product development after basic research and elemental technology development.
In research laboratories and elemental development organizations, new technologies are explored in a big picture, and the prospects for practical application are set.
If these activities are completely seamless, and there are no quality problems that can occur once the drawings are done, then set-based development may not be necessary.
However, in many companies, what is passed down from the research institute or element development organization to product development is the completion of a single technological unit or element, and there are usually still unknowns, unknowns, and risks that remain in order to turn it into a product.
In other words, even if a new technology is shelved from the research laboratory or element development department, there are still many unknowns and challenges left in the product development stage.
In addition to the technology inherited from the research labs or the element development department, you should have some stretch goals, such as wanting to slightly increase the conventional specifications in order to increase customer satisfaction, or to make a good product through ingenuity at the product development level.
By taking the approach of building up knowledge of these unknowns and challenges through the learning cycle of set-based development, we can ensure that the project is promoted toward the goal.
The misconception that it will take extra time and cost more than before
I often hear people say, “If we don’t decide on a method and leave multiple methods to experiment with each element, it will take a lot of time and cost.
The idea is that it would be much faster to focus on one method and build a prototype using that method once it is decided.
I think they believe this because they feel secure in the fact that they have been doing it that way for a long time, and they intuitively believe that it is faster.
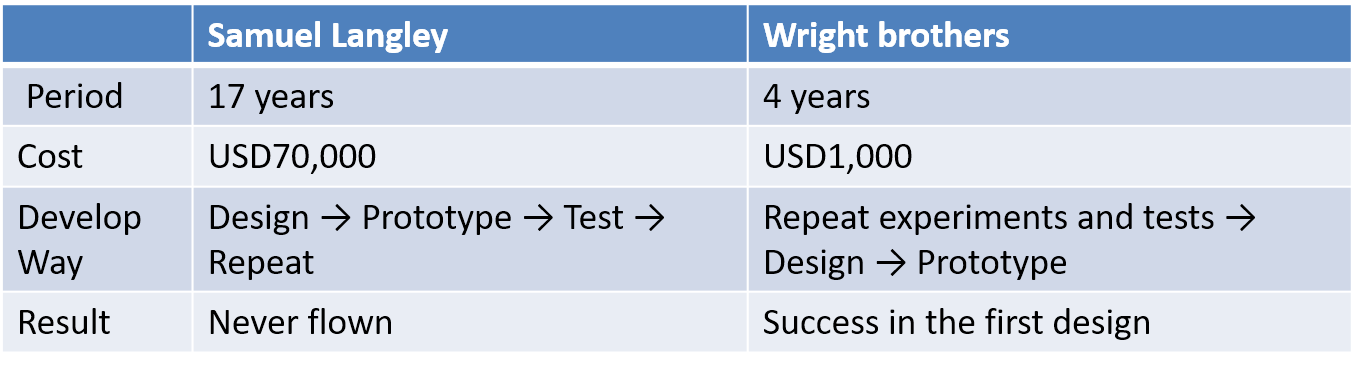
Many people have tried to make airplanes fly. Among them, a man named Samuel Langley took the approach of building prototypes and then flying them, and as a result, he was unable to make a single successful flight in 17 years.
The Wright brothers, on the other hand, succeeded in flight with a single prototype by repeating basic experiments and building up their knowledge without prototyping.
There are many other examples of shortening time by set-based development.
I think this is a good example of how we can misunderstand the true nature of things if we are caught up in conventional wisdom and fail to break free from our assumptions.
Of course, there are obstacles, but I hope that you will once again calmly consider whether the method of building a mud boat and tinkering with it is superior to the method of designing a high system from the beginning.
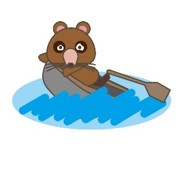
The question of whether small experiments are difficult
For organizations that have been developing their products by building prototypes of the entire product, an inexpensive, small-scale experiment (MVE: Minimum Viable Experimentation) to stop prototyping the product and learn only the knowledge they want to acquire may indeed be a hurdle.
You’ve never done it before, so you don’t know how to do it.
I think we should consider that this idea itself is the result of the fact that we have been developing only minor changes to existing products.
In order to develop a completely new product, it is more risky to make a prototype of the entire product first.
Since we are entering an unknown world, if we do not proceed step by step, leaving our footprints behind, not only do we risk failure, but it would be like making a one-shot product that cannot be reproduced, and we would not even be able to maintain the technology.
The essence of product development is.
- Understand what it is that you don’t know
- Change what you don’t know to what you do know
I think it is a repetition of these two steps.
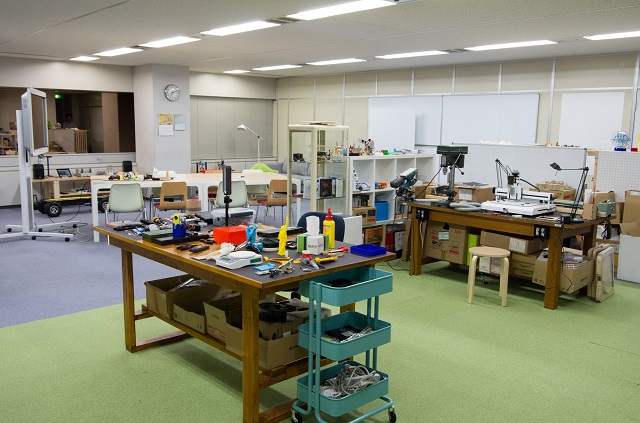
In order to make small experiments a habit, I think it is important to go back to the basics of manufacturing and create an environment where people can “try it and show it” or “let it happen” by making a simple device and trying it out when they get an idea.
I think the basic idea is to provide a good “laboratory” and to have a company-wide awareness that innovation can occur in the “laboratory.
Objection that it is not consistent with existing processes
The most significant obstacle may be the objection that the existing process cannot or does not want to be changed.
The figure below shows the phase-gate development process that many companies have adopted.
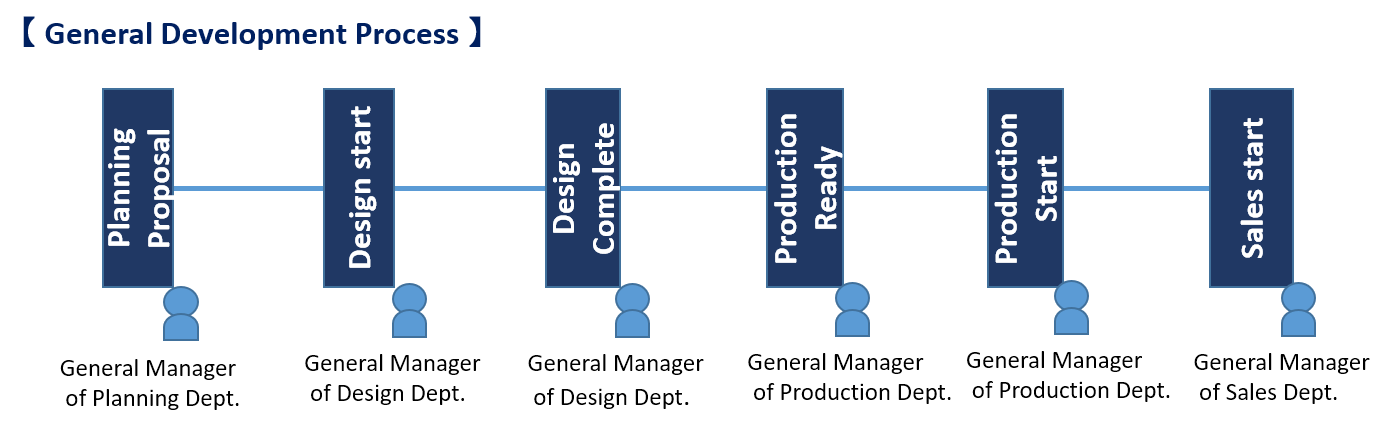
In the planning phase, the planning department is responsible for determining the product plan.
In other words, if the method is not decided first with a set-based approach, conflicts will suddenly occur.
Once the product plan is decided, the head of the design department is responsible for verifying the design in a limited time.
This is where the idea of set-based development, which is to fill in the technology while learning, doesn’t match up well.
In set-based development, a charismatic leader, the chief engineer, leads the entire process, building up the technology and conceptualizing the product to achieve customer satisfaction at the same time, abandoning the phase-gate approach.
In other words, a drastic change in the development process is required.
The question is how to judge the risk of changing the process, the question of whether changing the process will be effective, and the expected results as an organization.
If top management can’t make decisions, they can’t get to the starting line of reform
Set-Based Development is an excellent method to shorten development time and obtain rework-free development by understanding customer value, innovating, and eliminating development waste, but as mentioned above, there are obstacles such as misunderstanding and difficulty in gaining organizational understanding.
However, as mentioned above, there is an obstacle of misunderstanding and difficulty in gaining the understanding of the organization. If the top management of the organization judges that the foreseeable obstacle is fatal to the organization and the results to be obtained are not promising, then this reform should not proceed.
However, if the obstacle is an assumption or a fear of stepping into the unknown, then I believe it can be overcome.
If, for example, middle managers or engineers in the field start to think that they want to promote organizational reform using the set-based approach, the biggest problem is how to propose it to the top
In the next step, I will explain how to convince the top management of the set-based reform.
How to logically persuade top management to proceed with set-based development

In order to promote any kind of reform in an organization, not just set-based, you need the understanding of the people around you, especially the consent and support of top management.
However, as mentioned above, there are many misunderstandings and obstacles in promoting reforms using Set-Based, the theme of this project.
In our company, we use TOC (Theory of Constraints) thinking process for organizational reform and organizational problem solving.
TOC (Theory of Constraints) considers that when you are trying to do something in an organization, there are six layers of resistance (see the figure below).
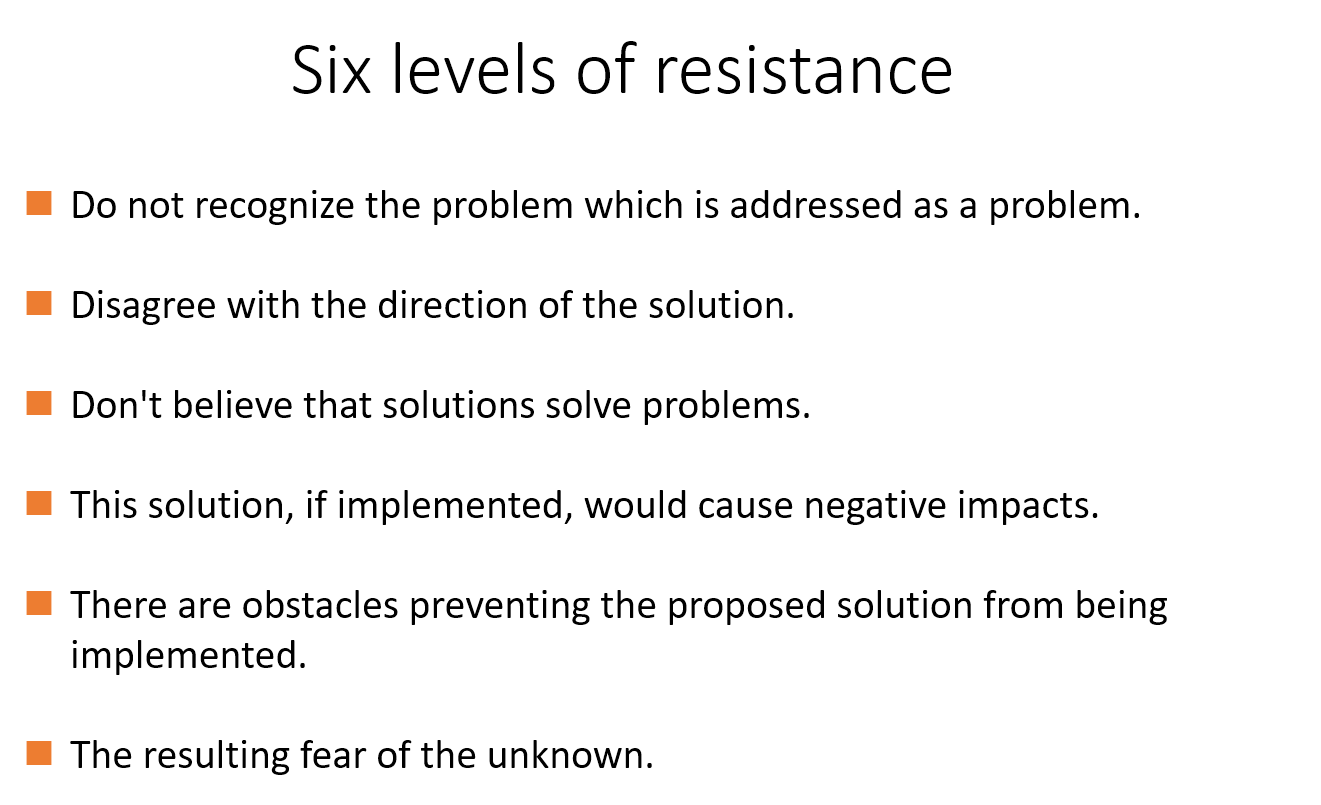
Among the misunderstandings and obstacles, the question, “Aren’t we talking about separating element development from product development after all?” means that we don’t agree with the direction of the solution, and the misunderstanding, “Won’t it take extra time and cost?” seems to be connected to the fact that we don’t think the solution will solve the problem.
Furthermore, the suggestions that “small experiments are difficult” and “not consistent with existing processes” imply that there are obstacles that prevent the solution from being implemented.
The only way to overcome these resistances in the organization is to persuade them, right?
So how do you persuade? People are not easily convinced by verbal persuasion or qualitative explanations.
In order to persuade top management, you should prepare your proposal with the following points strongly in mind.
- Demonstrate the objectivity and credibility of the current situation analysis with data and logic
- Understand the thoughts of the top management and the key issues they want to achieve
- Propose a story to solve the top management’s key issues
- Provide concrete examples of successful best practices (e.g., set-based)
- Carefully analyze the side effects, obstacles, and risks of the proposed measures and specify countermeasures
Let’s look at them one by one.
Show the objectivity and credibility of the current situation analysis with data and logic
Strategic thinking is very important when you are trying to reform something.
When thinking strategically, the first thing to do is to analyze the current situation accurately and objectively.
If we cannot accurately describe where we stand now, we will not be able to reform ourselves.
We need to measure what is currently happening and what we perceive to be the problem, and convert what we can into data.
For example, comparing the number of quality problems at each stage and the time it takes to solve them between the past and the present will help us objectively understand how the situation has changed.
The frequency of occurrence of similar problems can also indicate problems where the experience of the organization is not being utilized or where “knowledge” and “wisdom” are not being shared, leading to an explanation of the effectiveness of set-based and A3 reports.
If we start to have data-centered discussions on a regular basis, we will be less likely to make assumptions, which will lead to healthy reform activities.
After the organizational problems have been listed with data, another important thing is to find the root cause of each problem.
A common bad example is to list multiple problems and try to do something about each one.
It is a mistake to try to take action on the phenomenon that is occurring without analyzing the root cause.
In the problem solving framework using TOC (Theory of Constraints), multiple problems are considered as bad symptoms, and the bad symptoms are considered to be causally connected to each other.
In other words, a chain diagram of problems is created based on the idea that bad phenomena originate from a small number of root problems and are manifested as many symptoms in a negative chain. (This is called a “status quo tree.”)
If we follow the root of the chain diagram (the current situation tree), which is connected by a chain of cause-and-effect relationships, we will find that it is the fundamental problem of the organization.
For details on how to create a status tree, please refer to the separate article “Structuring Problems in Development Organizations“(a series of five articles).
Understand the thoughts of top management and the key issues they want to achieve
The common business goal of all companies is to make a profit, in other words, to keep making money.
Each manager may have a different approach to the absolute challenge of remaining profitable.
There must be a method of approach that the top management of the company considers, or a second-level goal for making a profit.
This should be expressed in the vision, management policy, and mid-term business plan, and you should recall the messages you usually receive and understand them well.
If the proposal has a solid answer to how this proposal relates to the goals and basic policies that the top management is aiming for, it will be a reform that will be understood by the top management and that will bring the whole company together when it is implemented, leading to the ultimate goal of improving profits.
For example, it is important to make a proposal that is in line with the top management’s idea, whether it is to expand profits while slowly shifting from existing to new businesses, to increase the cost of the existing product lineup, or to expand profits by challenging a new business model.
It does not mean that you have to bend your own ideas to make a proposal, but rather that you have to think of your proposal as a way to make the top management’s ideas come true together.
Propose a story that solves a key problem at the top
When you make this suggestion to the top management, if their thoughts are at a higher level, as in the previous paragraph, then you can say, “If we implement set-based development, we can reduce the development time by 40%.”
If you make a proposal like this to the top management, but their thoughts are at a higher level, as in the previous paragraph.
“So what?”
Or, if the scenario of a 40% reduction in development time, followed by an increase in sales opportunities due to faster time to market, is understood, a skeptical top management may say, “Why is that possible?
“How is that possible?”
They would say.
As the saying goes, “Rome is not built in a day,” and the bigger the challenge, the harder it is to reform.
The top management is well aware of this.
So, we should explain the scenario of the reform in a logical and simple (not overly complicated) way.
The figure below is called the Future Tree, which is used in the TOC (Theory of Constraints) problem solving framework.
It illustrates how the situation will change for the better through a positive chain of events, starting from a few measures (2-3) (called injections in TOC) to solve the fundamental problems of the organization discovered in the current state tree.
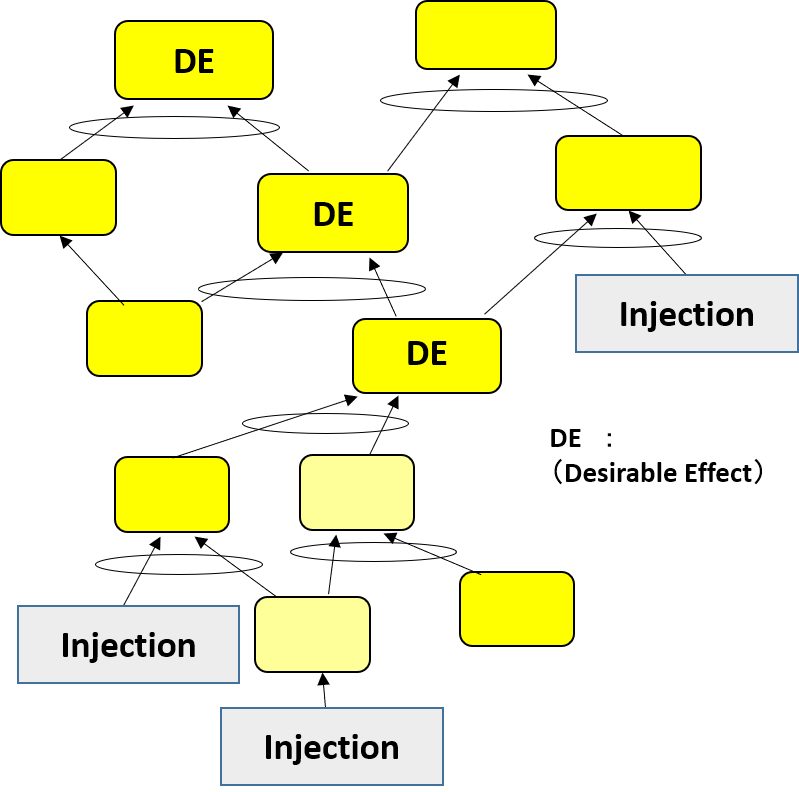
From Injection, cause-and-effect logic can be used to show the top future to aim for.
For more information on how to find injections (measures) from the root problem, please refer to “Structuring Problems in Development Organizations (Part 4)“.
Specific examples of successful best practices (set-based development)
So far, I have explained the methodology of how to persuade the top management logically, showing some basic ideas of TOC (Theory of Constraints
The TOC (Theory of Constraints) methodology is beyond the scope of this article. If you are interested, please refer to the separate article “Structuring Problems in Development Organizations“.
In this section, I will talk about how to get the top management’s agreement on set-based development.
In the previous section, I talked about measures (injection) for the root problem. Injection is expressed as what kind of state to create based on a deep understanding of the advantages that can be gained from set-based development.
As you will see if you fully understand the advantages of a set base, here are a few examples.
- Make a list of all unknowns, challenges, and hypotheses before starting development
- Do not decide on a method until the hypotheses have been verified
- Make decisions with the entire team while building up knowledge through learning results
- Make an A3 report of the “knowledge” in the company and proceed with development based only on the “knowledge”
In short, instead of adopting a form of set-based development, we propose to draw out the good points of the set base and apply them to our company.
It is a sense of taking the good points from the set base as a theory.
Not all things can be accomplished at once.
Some things can be accomplished with improvement over time and through repetition.
When you incorporate the good points of the set base, show at the top what specific results can be expected in each point.
For example, by developing a list of unknowns and challenges, quality problems due to lack of prior consideration will be reduced to zero as much as possible, and so on, explained as a cause and effect relationship.
If there is evidence of this in other companies’ case studies, that is the most persuasive, but if it cannot be explained in the form of a case study, declare that it is a hypothesis and then convince people that it is a credible hypothesis.
By breaking down the elements of the set base and convincing the members, including top management, of its benefits, they will be able to find new solutions of their own.
By continuing to make changes step by step, we will make major innovations.
It is important for all of us to have a clear image of the idea of accumulating results one by one, that is, concrete examples of success.
Carefully analyze the side effects, obstacles, and risks of the proposed measures and specify countermeasures
As explained in the section on misunderstandings and obstacles, trying to implement all set-based development as a theory leaves many concerns for the organization.
Showing that you are fully aware of the obstacles, side effects, and risks will give top management a sense of security.
It also proves how deeply you are thinking about it, but the idea itself is set-based, isn’t it?
The set-based approach is to make a list of things you don’t know and challenges and learn them one by one, so in the case of reforms, it means to identify obstacles, side effects, and risks and carefully eliminate them one by one as you proceed.
It would be unacceptable for someone who recommends set-based reform not to have an idea of set-based reform.
The TOC (Theory of Constraints) framework includes a process of planning while considering side effects and obstacles in advance.
In our reform, we will use the TOC framework to deal with side effects and obstacles.
However, even if we do not use the TOC framework, the essential idea is the same.
When we think of a positive chain of events, when we start with an injection and change one thing, something good happens as a result, and from that good result, another good thing happens.
When we think of a positive chain of events, we check for side effects, pick up the possible side effects, and think of new measures to deal with the picked up side effects.
In TOC, we call it negative branching, but it is not that difficult to predict the side effects and think of a response without using TOC.
As for obstacles, when we think about implementing a certain measure (injection), we identify that it cannot be achieved immediately and that we need to remove obstacles to achieve it as we go along.
For example, if we don’t want to achieve the state of “making decisions while learning,” we need to change the existing relay-type phase-gate process into some other form, or we need to determine who will lead the learning process. In Toyota’s style, this would be the chief engineer, but we also need to develop a new leader who will control the learning cycle, even if he or she doesn’t have as broad a responsibility as the chief engineer.
In this way, it may be necessary to set milestones in the middle before achieving the desired state.
By picking up obstacles and setting milestones to overcome them, we can create a highly feasible plan for all the measures (injections) to be achieved.
Summary
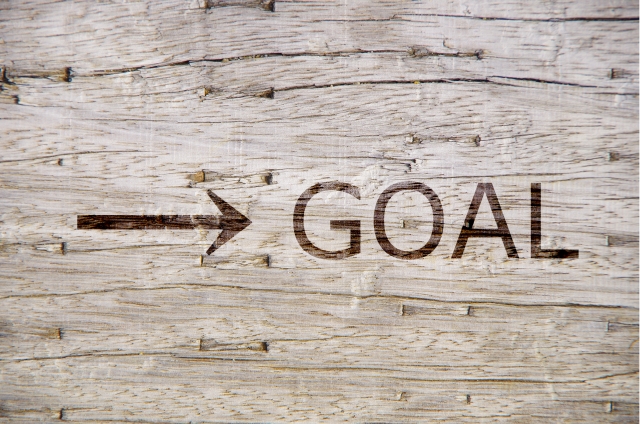
I hope you have understood that there are some hurdles in applying the Toyota Lean development methodology, not only to set-based systems, but also to actual organizations.
Naturally, it contains many hints for solving current problems, and if done well, it can be a great step forward in the ultimate goal of a company, which is to keep making money.
Given the fact that it is an ideal theory, it is easy to foresee the objections from those who oppose it, and unless the top management can be successfully persuaded to suppress the objections, the reform cannot even get started.
In this article, I have explained some of the misconceptions and obstacles to practice, to the extent that they are easily predictable, and talked about a simple guide to persuading top management logically.
The bottom line is that you need to put together a solid strategy to achieve the objectives of the innovation and motivate top management to do so.
I am planning to put together an article on how to formulate a development innovation strategy in the next opportunity.
Please look forward to the more detailed explanation of how to logically persuade the top management that I have described in this article.
We also use Lean Development Methodology and Job Theory to reform the development organization by
- Structuring the current organizational problems and identifying the root causes
- Setting goals and developing strategies to achieve them
This service is provided in collaboration with the client company.