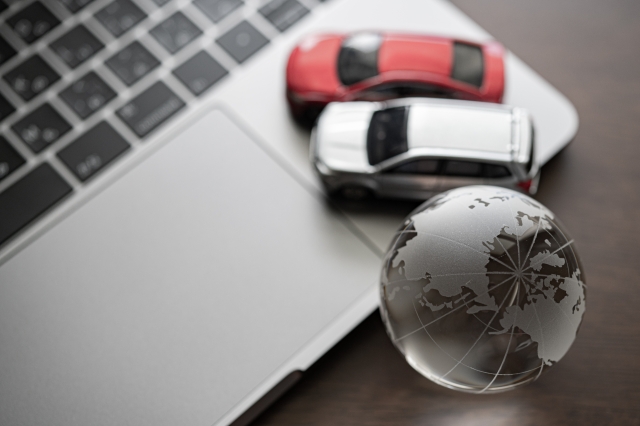
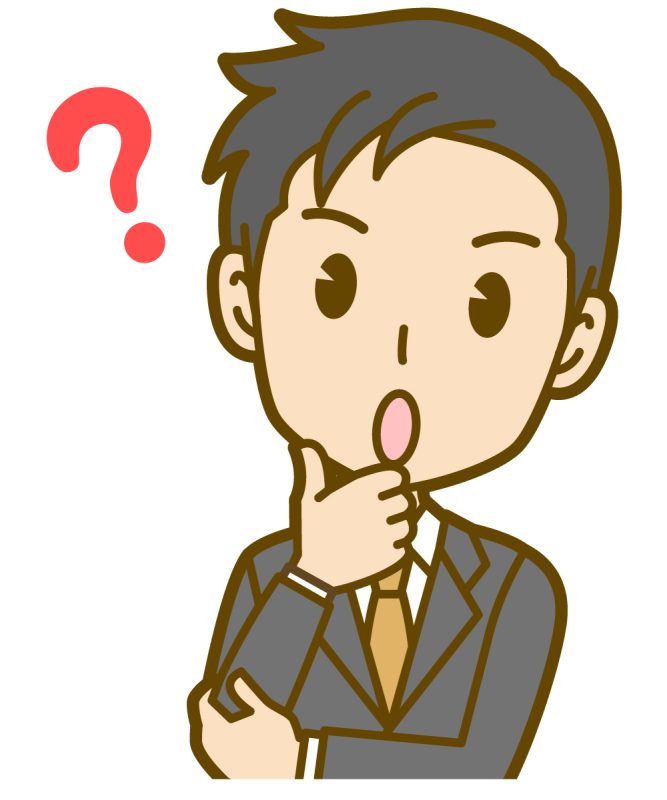
トヨタが勝ち組なのはわかるが、製品開発においてトヨタから学んで本当に成功するにはどうするか?
日本の大企業がかつての勢いを無くす中、トヨタだけはグローバルで勝ち続けている。リーン製品開発手法、チーフエンジニア制度、A3報告書など、トヨタの製品開発の秘訣について様々な情報も流れているが、トヨタの開発手法を取り入れて成功した事例についてはあまり情報がない。リーン製品開発をどう実践すべきなのか、あるいはトヨタが勝ち続けている理由はもっと違う所にあるのか?本当の理由を知りたい!
トヨタがグローバルで勝ち続けているのは何故なのか?
リーン生産方式を学んで取り入れ、成功している企業があることは広く知られています。
今、製品開発においても他の製造企業の開発とは一線を画した開発手法であることが、アレンウォード著「リーン製品開発方式」によって紹介され、開発革新を目的にリーン製品開発手法を取り入れようとする企業も増えてきています。
しかし、リーン生産にしてもリーン製品開発にしても、なぜそれが企業の成功に結び付くのか、その本質を捉えなければ本当の意味での成功は覚束ないと思います。
トヨタ成功の秘訣を本当に理解するためには、それぞれの手法や考え方が生まれた背景、そしてそれらが受け継がれている歴史的な流れを理解する必要があると思います。
本記事の内容
初代クラウン開発から受け継がれる強いリーダーシップ(チーフエンジニア制度)
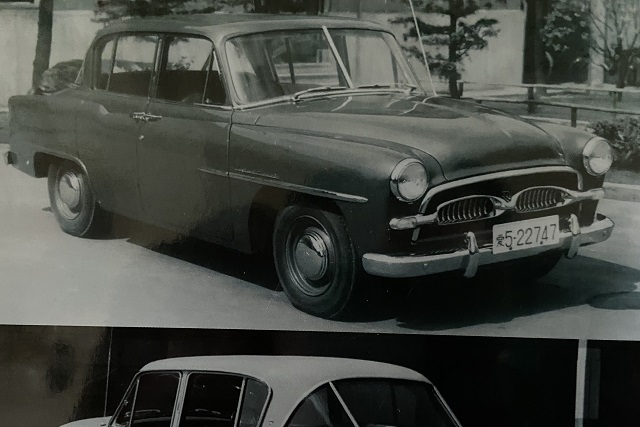
大野耐一さんがトヨタ生産方式というトヨタのものづくりの礎を築いたことは広く知られていますが、製品開発の強さの背景は実はあまり知られていないのではないでしょうか。
トヨタ製品開発の強さのルーツは、初代クラウンの開発にあるといわれています。
自動車が発明されたのが1769年、一般に自家用車が普及するきっかけのなったT型フォードが発売されたのが1908年、それから40年余りたった1950年ころ、日本企業だけで国産の自家用車を開発するのは技術的に不可能だと考えられていたそうです。
そしてその常識を覆して見事に、欧米に負けない国産自家用車として生まれたのがトヨタの初代クラウンというわけです。
初代クラウンは、1952年1月に開発がスタートし、3年後の1955年1月に発売されています。
この開発を行ったのが、初代のチーフエンジニア(当時は主査と呼ばれた)である中村健也さんと開発チームの皆さんです。
中村さんとそのチームが様々な困難に打ち勝って、初代クラウンが世に出るまでのストーリーは、桂木洋二著「初代クラウン開発物語」に詳しく書かれています。
トヨタの2代目社長であり、実質的に現在のトヨタ自動車を作り上げた豊田喜一郎は、日本でアメリカに負けない自家用車を開発することに強い拘りを持っていたようで、全社に対して3年でアメリカに追い付けと激を飛ばしたそうです。
この激を受けて、大野耐一さんがトヨタ生産を生み出していくのですが、同時に中村さんも、自分たちの力だけで自家用車を開発することに強い想いを持っていたようで、経営トップと現場リーダーの力がシンクロしたことで、初代クラウン開発が成功し、トヨタがそこから躍進していくことに繋がったように思います。
トヨタの強さは生産方式にあるというのが多くの人たちの見方かもしれませんが、実は初代クラウン開発の成功はトヨタの開発力を強靭なものにし、それが現在まで脈々と受け継がれているのではないか、ということは実はあまり知られていないのかもしれません。
リーダー中村主査の元で、開発チームは様々な難問に立ち向かっていきます。
中村さんは、とても変わった人だったことが知られていて、あまり人付き合いが上手ではなく、一人で黙々と本を読みあさり、自分が先頭にたって問題解決をしていくタイプの人だったようで、そういう意味ではチームをまとめて大きな仕事を成し遂げてい行くという、今でいうリーダーのお手本のような人ではなく、自分が率先することで背中を見せてチームを引っ張る人でした。
中村さん語録というのがあり、中村さんの製品開発に対する強い想いが表れているので紹介しておきます。
- うまくいくかいかないかわからないから開発するんだよ
- 開発は先の見えない夜行列車。知恵と度胸で突き進め
- 成功の確率が50%だったら絶対やらなきゃいかん。30%でも挑戦する価値があるよ
- 下手な指示は部下の独創性を殺すだけだ
- 開発に最も大切なものそれは自由だ。与えられた自由ではなく獲得した自由でなくてはならない
- 何事も安全第一でやっていては、技術の向上はないし、他社よりも先に行くことはできない
これらのことがトヨタ製品開発のルーツだと考えられます。
そして、初代クラウンの開発で、中村主査をサポートしたのが長谷川龍雄さんという方で、この方は初代クラウン開発の成功体験を受け継いで、その後、トヨタのヒット商品となったカローラで主査を務めます。
長谷川さんは、その後、主査を取りまとめる仕事に就き、下記のような「主査たるものの10か条」というのを設定して、トヨタ製品開発のDNAとしていったのだと思います。
- 査は常に広い知識、見識を学べ
- 主査は自分自身の方策を持つべし
- 主査は大きくかつよい網を張れ
- 主査はよい結果を得るために全知全能を傾注せよ
- 主査は物事を繰り返すことを面倒がってはならぬ
- 主査は自分に対して自信(信念)を持つべし
- 主査は物事の責任を他人のせいにしてはならぬ
- 主査と主査付は同一人格であらねばならない
- 主査は要領よく立ち回ってはならない
- 主査に必要な資質――知識、技術力、経験、洞察力、判断力、決断力、度量、感情的でなく、冷静であること、活力、粘り、集中力、統率力、表現力、説得力、柔軟性、無欲という欲(人格)
リーダーとしての中村さんの仕事のやり方が見本になったわけではなく、中村さんのどんな難しいことにも、あきらめずにリーダー自らチャレンジし続けるという開発に対する強い想いがトヨタ製品開発の出発点で、それが長谷川さん始め次の世代のリーダーたちに受け継がれ、さらに長谷川さんによって、開発リーダーしての心構えや行動指針が明確に示されることで、トヨタのDNAが形作られていったということだと思います。
そして時が過ぎ、中村健也さんから何代か後のチーフエンジニア(主査)経験者である北川尚人さんは、その著書「トヨタチーフエンジニアの仕事」の中で、トヨタのチーフエンジニアを育成するための特別な育成プログラムなどがあるわけではなく、歴代の先輩チーフエンジニアの背中を追いかけて育つということをおっしゃっています。
トヨタの状況を学び、自分自身でもリーダー育成に取り組んできた経験から、会社の中で強いリーダーを継続的に生み出す方法は、強い背中を受け継いでいくことだというのが私自身の確信でもあります。
トヨタ生産方式から学んで徹底的にムダを排除する企業文化を作る

トヨタの製品開発のDNAが形成された経緯を理解いただいた上で、トヨタの本当の強さを考える上では、やはりトヨタ生産についても見ておくべきかもしれません。
トヨタの生産方式はリーン生産とも呼ばれますが、特にカンバン方式が有名で、トヨタ生産というと”カンバン方式”と考える人も多いのかもしれません。
しかし、トヨタ生産方式を生み出した大野耐一さんは、その著書「トヨタ生産方式」の中で、トヨタ生産方式=カンバン方式と考えられていることをとても遺憾に思っているとおっしゃっています。
大野さんは、トヨタ生産方式は、
- ジャスト・イン・タイム
- にんべんの付く自働化
の2つなのだとおっしゃっています。
ジャストインタイムは「必要なときに必要なものを必要なだけ」、にんべんの付く自働化は人の知恵で機械化を進める、ということであり、その心は、「人の知恵で徹底的にムダを排除する」ということなのだそうです。
大野さんが言いたいことは、カンバン方式のような「誰かが」成功した「手法」を実践することでは、絶対にうまく行かないということなのだと思います。
企業ごとの課題にチームで向き合い、自分たちで考えて徹底的にムダを排除するためにどうしたらいいかを考えて生まれたのがトヨタ生産方式であって、その本質は「出来上がった生産手法」ではなく、自分たちで考え抜いて課題を解決してきたプロセスにあるのだということです。
ここで、トヨタ生産システム(TPS)を学んで大成功した企業のお話しを少ししたいと思います。
台湾企業で、産業機器を製造・販売するKeyArrowという会社があり、そこの王CEOは、リーン生産方式を自身で学び、自身が先頭に立って会社の改革を実行し成功されました。
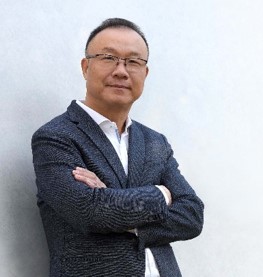
王CEOは、リーン生産方式を指導するコンサルタントを雇い、自らもリーン生産の何たるかを深く学んでそれを自社で実践した結果、自社製品(産業用機器)の生産リードタイム(材料入荷から製品出荷までの時間)を4年間で6.6日から1.4日に改善し、さらに3年かけてなんと30分にまで改善したのです。
更に、在庫(部品、仕掛、完成品在庫すべての年間売り上げに対する比率)を約20%から8年間で1%に改善し、さらに改善を続けて最終的に0.6%、つまり在庫回転率でいうと150回という驚異的な数字を達成していきました。
トヨタ生産を学んで、王会長が最初にやったのは、自社だけでなく、部材メーカーと顧客を巻き込んだ全体最適で無駄を省くということです。
王CEOの会社を訪問したときに、CEOが最初に言ったのは、「例えばお客さんから10月30日に30個の製品を納品するように依頼があったとしますね。ではお客様は本当に10月30日に30個の弊社の製品(お客さんにとっては部品)を必要とするのでしょうか」ということでした。
「本当に必要なのは、11月1日に8個、2日に7個...とか、数日に分けて使うことが多いと思いませんか?」と続けます。
CEOが言いたいのは、だったら本当に必要な日にちに合わせて納品させてもらえれば、弊社の生産はもっと楽になるということなのですが、もちろん、どちらも余裕がなくなるので、お互いの信頼関係がなければ出来ないということはありますが、さらに言うと、細切れに納品することで輸送に関して逆に無駄が出てしまうという懸念があることに気づきます。
すると王CEOはにっこり笑って、だから部材メーカーや顧客企業、さらに近隣の企業を巻き込んで、定期的な輸送システムを作り上げたのです、と言ったのです。
例えば一時間ごとに近隣を周回する定期輸送便を設定して、それと各社の生産計画を合わせることで、自社だけでなく、顧客企業も仕入先も、さらに近隣の関連企業もすべてが恩恵を被ることができ、全体での無駄を省くことが出来るわけです。(王CEOの改革の詳細は、別記事「リーン生産、リーン開発から学び続け変革し続けるカリスマ経営者から学ぶこと」を参照ください。)
王CEOの改革は、リーダーが自ら学び、率先して改革を引っ張ったことはとても大きなことですが、それ以上に、全社員がやる気に満ちていて、リーダーからの権限移譲もあり、全員で改革を進めたことが最も大きな力になったように思います。
工場を見せてもらい、現場の社員の方とお話ししていると、1980年代の日本企業がTQCを学びながらQCサークルで全社員で会社を変えていった姿と重なって見えました。
この企業と王CEOがやったことは、決してトヨタの真似をしたのではなく、トヨタのやり方をヒントに、自分たちの課題を自分たちで見つけて、それを解決していくことで、強い会社を作っていったのだと思います。
社員の一人に、「ここまで改革したらもうやることありませんね?」と言ったら、その社員はにっこり笑って、
「まだまだやるべきことはたくさんあります。私たちはグローバルで勝てる企業になるんです。」
と言っていた自信に満ちた顔はとても印象的でした。
優れた開発システムと人材育成の両輪を維持するDNA
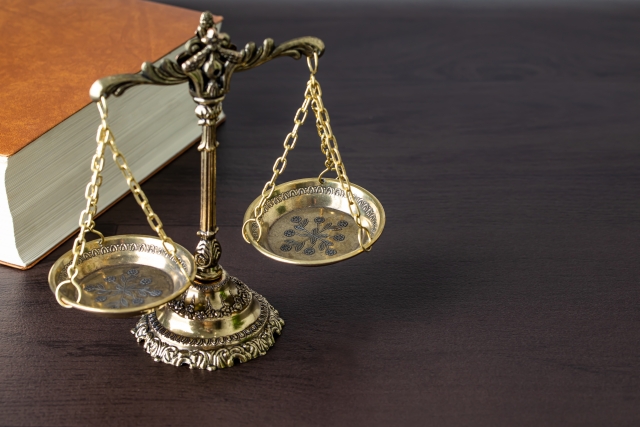
海外EMS企業で、多くの企業と製品開発や生産の仕事をしてきて、各社の製品開発のプロセスやシステムは、そんなに大きく違わないと思う反面、リーン生産(トヨタ生産方式)のような世界で見本と認められる方式が、製品開発の領域では見当たらないと考えている企業は多いと感じています。
自社のやり方は門外不出だと考えている企業も多いのかもしれません。
長い歴史の中で、それぞれの企業の経験(失敗も成功も含めて)から生まれた信じるべき開発システムですから、そこを根本的に変えるということはなかなか思いつかないという側面もあると思います。
もちろん、それぞれの企業ではそれぞれの課題も認識していて、改革ということを忘れたわけではないと思うのですが、例えば「品質問題が多発している」とか「日程遅れが常態化している」などの課題に対して、いろいろと手を打ってきているけれども、何年経っても状況は変っていない、ということはありませんか?
だからといって、開発システムを根こそぎ変えてしまうということは、リスクが大きすぎるし、何より見本となる開発システムが見当たらない、ということになるのだと思います。
そこに、最近になってトヨタのリーン製品開発(アレン・ウォード著「リーン製品開発方式」参照)というのが良さそうだという情報が流れてきて、では我々も取り組んでみようということになるのですが、初代クラウンが成功した背景、大野耐一さんの言う本当のリーン生産の考え方、そしてKeyArrow社の王CEOが実践した改革の本質などを考えると、手法や方式そのものに飛びつくのではない本物の改革を考えるべきと強く思うわけです。
確かにトヨタ生産方式のジャスト・イン・タイムの考え方は、トヨタだけでなく世界の製造業を大きく変えることになる素晴らしい考え方だと思います。
それまでの常識をぶち破って、生産の本質を追及した結果に生まれたもので、後から着いていく人たちはやり方をコピーするのではなく、考え方を取り入れて後は自分たちで切り開くことで成功していくわけです。
製品開発もまったく同じことで、トヨタの開発方式やプロセスをコピーするのではなく、その方式に至った考え方を学び、自分たちで考えて切り開いていくことが必要なのだと思います。
とすると、製品開発革新を進めるためには、成功している開発システム(トヨタなど)の本質を深く理解することが第一歩で、そこから自分たちの課題を解決するための自分たちのやり方を考えていく力が必要になるということです。
つまり、理解する”人”、考える”人”、そして実行する”人”が一番重要で必要なことなのだということです。
製品開発に限らず、企業改革を計画し、実行するには何よりもまず、人材を確保すること、そして優秀な人材を継続的に生み出すDNAを作ることが大事だと思うのです。
トヨタの大野耐一さんは、多くの優秀な後継者を育てた人でもあったようです。
一方、初代クラウンのリーダーであった中村健也さんは、その背中で大事なことを残したのですが、彼が直接後継者を育成したのではなく、クラウン開発を成功させるために中村さんをサポートした長谷川さんやその他の人たちによって自然に引き継がれていった側面と、長谷川さんたち中村さんの後のリーダーたちによって、明示的にDNAが作られていったのかもしれません。
結論としては、自社の開発を強い製品開発システムに変革するためには、
- 優れた成功事例に対する深い理解(本質的な考え方)
- 本質的な考え方を自社で実践できる人材育成
の両輪が必要なのだと思います。
そして、トヨタの製品開発などの成功事例、ベストプラクティスを学ぶには、表面的な手法、プロセス、体制などにフォーカスするのではなく、その成功事例が生まれた歴史的背景を学ぶことが大事だと考えています。
初代クラウン開発には、無謀だと言われながらチャレンジして、一つひとつの難問をクリアしていった”人”の力、”リーダー”の力があります。
中村さん語録の最後の一行、「何事も安全第一でやっていては、技術の向上はないし、他社よりも先に行くことはできない」は、実は多くの企業にとって耳の痛い話であると思うし、既存事業を長い間継続することが収益のベースになっている多くの企業では、”失敗を許さない”体質が出来上がり、そしてそれが”優秀な人材”を育てることを邪魔していて、その結果、開発における諸問題が長い間解決できない状況になっていると考えると、いろんな辻褄があうように思います。
トヨタのリーン製品開発手法の本質を捉え、
若手エンジニアのモチベーションによる改革を目指し、
トヨタの真似でない独自の世界観で
組織改革に挑む姿を描いています。
詳しくは、「製品開発組織の常識をぶち壊せ!!」出版のご案内を参照ください。
自社の問題の本質を捉えて、リーン開発の考え方を取り入れる
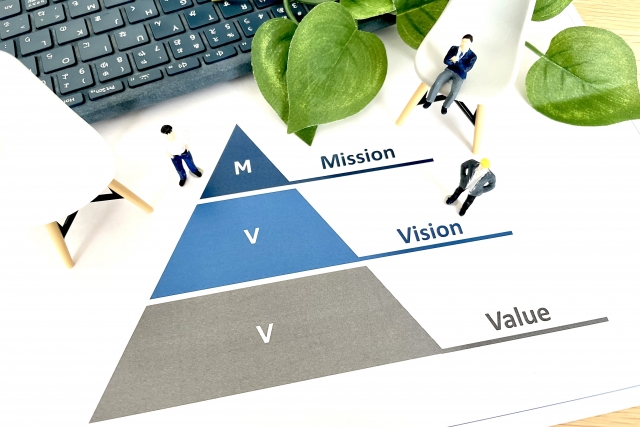
世の中の成功事例をそのまま実践することではなく、大事な考え方が生まれた歴史を含めて、しっかり学ぶことの重要性、そして人材育成の重要性についてお話ししてきました。
最後に、製品開発システムや組織の改革を行う時に、もう一つ大事なことをお伝えしたいと思います。
それは、自社の現状の問題を正確に捉えるということです。
正確に捉える、つまり本質を捉えることの反対は、表面的な捉え方をするということです。
当たり前じゃないかと言われそうですが、実は多くの企業が表面的な捉え方で失敗していて、しかもその失敗に気づいてさえいないということを申し上げたいと思います。
簡単に言うと、起きている現象だけを見て、その現象を抑えることで乗り切ろうとして失敗するということです。
実は政治の世界でも同じようなことって起きてますよね。
例えば、日本の平均年収の世界ランキングはここ20年くらいで少しずつ落ちていて、現在は主要38か国の中で21位であり、20位の韓国よりも下のランクになっています。
日本の生産性が上がらないのは、女性活躍が他の諸外国より悪いからだと、女性活躍のための政策を打ったりしますが、状況は変りません。
ある学者さんによると、日本の生産性が低い理由は、他の諸国よりも中小企業の比率が高く、経済効率が上がらない産業構造になっていることが本当の原因だと指摘しています。
そしてそれは、1964年ころ、日本がOECDに加盟したときに、その条件として「資本の自由化」を要求され、諸外国から中小企業を守る法律やシステムが次々に生まれたことで、中小企業天国が出来上がってしまい、それが今も続いていることだと指摘されています。
この議論の真偽はともかく、本当の問題を深く解析しないで、表面的な対策を打つ傾向は政府だけでなく、多くの企業にもリスクとして潜んでいます。
「品質問題の多発」、「日程遅れの常態化」などの問題をどう捉えて、どう対処しているか、それぞれの企業で異なるかもしれませんが、わかっているのは、有効な対策で成功した企業はあまりないということです。
例えば、「品質問題が多発している」という問題に対して、「では品質チェック体制を強化する」という施策を打つということを考えます。
それは、間違いではないのですが、「品質問題の発生」の原因は本当にチェック体制だけなのでしょうか?
品質問題がチェックされずに次工程に流れてしまう、ということの原因はチェック体制の甘さなのかもしれませんが、元々、なんで品質問題は開発に入り込んでしまうかという問題の本質を見ていないような気がします。
下図をご覧ください。
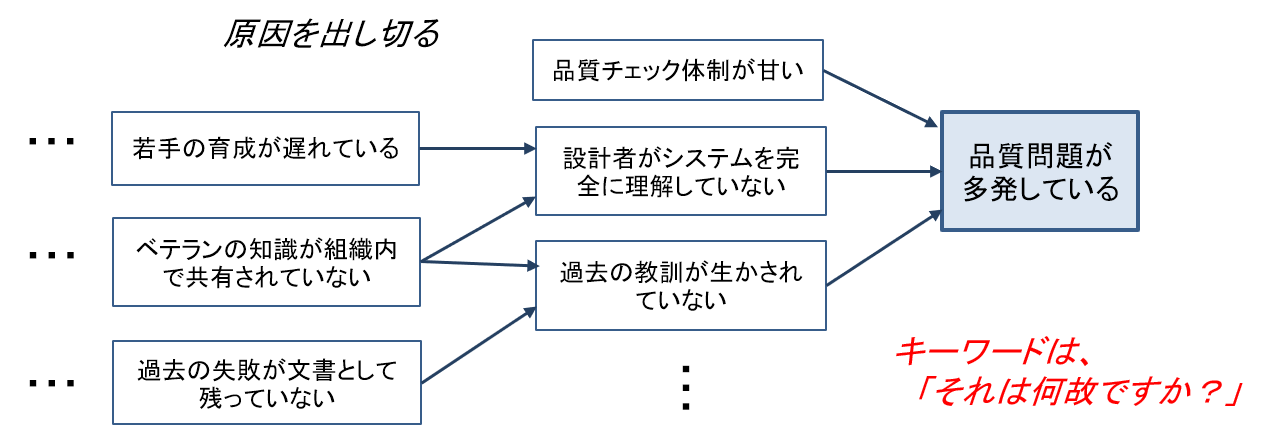
一つの現象に対して、「それは何故ですか?」という質問を繰り返してみると、実はいくつかの原因が見つけられることがあります。
品質問題に関しては、そもそも設計者がシステムを理解していないとか、過去の教訓が生かされずに同じような問題が繰り返されるなどの原因も考えられるかもしれません。
もっと言うと、設計者がシステムを理解していないとすると、もう一度「それは何故ですか?」と自問してみてください。
企業によっていろいろな原因に繋がっていきます。
組織の中の問題は、実は様々な形で繋がっています。
そして、その本質を捉えることが出来なければ問題の根本的な改善は不可能です。
トヨタのリーン製品開発を導入してみたい、と思ったのなら、まず、組織の問題の本質は何で、そこにトヨタの事例の何が解決につながるかをしっかりと考えなければ、解決には繋がりません。
弊社(フューチャーシップ)の組織改革の進め方は、まずは企業ごとの組織問題の根本、すなわち本質を突き止めるところから始めます。
そして、成功事例、ベストプラクティスとしてトヨタのリーン製品開発を学び、その考え方をどう自社に適用すれば問題解決が出来るかを考えていきます。
弊社の「連鎖式組織改革法」をぜひご活用ください。
この記事を気に入ってくれたら、下の”いいね”ボタンをお願いします!!